Computer Recyling Report Svtc
Download original document:
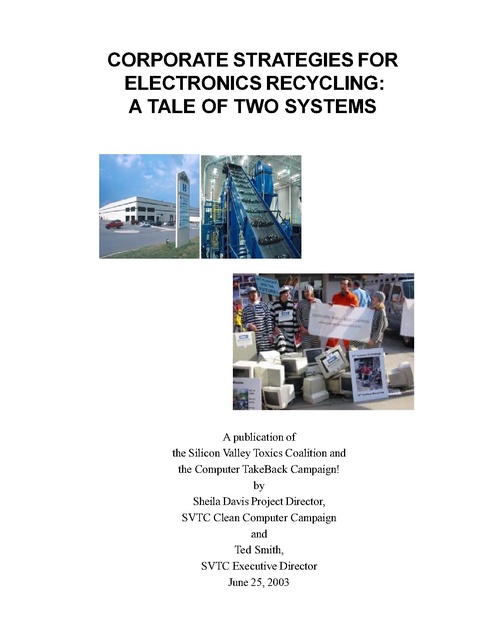
Document text
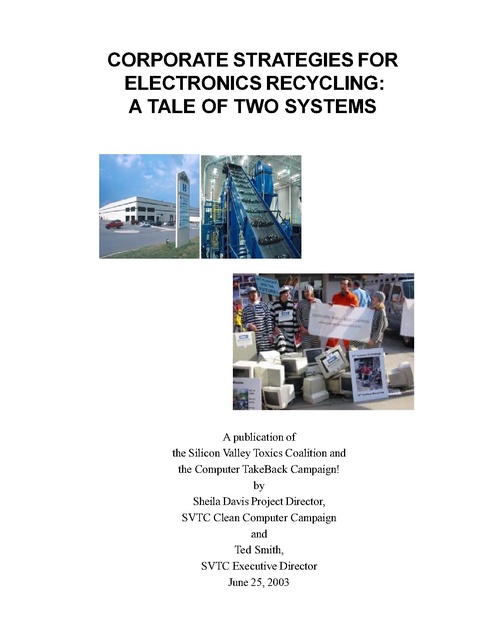
Document text
This text is machine-read, and may contain errors. Check the original document to verify accuracy.
CORPORATE STRATEGIES FOR ELECTRONICS RECYCLING: A TALE OF TWO SYSTEMS A publication of the Silicon Valley Toxics Coalition and the Computer TakeBack Campaign! by Sheila Davis Project Director, SVTC Clean Computer Campaign and Ted Smith, SVTC Executive Director June 25, 2003 CONTENTS I. EXECUTIVE SUMMARY 3 II. INTRODUCTION A. Background B. Report Structure 5 6 III OVERVIEW A. Health Impacts of Hazardous Waste B. Hazardous Materials in E-Waste and their Effects on Humans and the Environment C. Methodology 1. Overview of Electronic Disassembly, Recycling, and Processing and Workers Health and Safety Protections 1.A. Disassembly Process 1.B. Development of Efficient Materials Processing Systems 1.C. Worker and Environmental Protections 11 IV. SVTC TOUR OF RECYCLING FACILITIES A. Visit to HP - Micro Metallics 1. HP - Micro Metallics Recycling Warehousing System 2. HP - Micro Metallics Disassembly Process 3. HP - Micro Metallics Materials Processing System 4. HP - Micro Metallics Worker Protections 4.A. Health and Safety Program 4.B. Worker-initiated Protections 13 13 13 13 13 14 14 14 B. Visit to United States Penitentiary Atwater UNICOR Recycling Facility 1. UNICOR Warehousing System 2. UNICOR Disassembly System 3. UNICOR Materials Processing System 4. UNICOR Worker Protections 4.A. Health and Safety Program 4.B. Worker-initiated Protections 14 15 15 15 16 16 17 V. CONCLUSION 17 VI. ENDNOTES 19 8 9 9 10 10 11 Appendix A: Letter to Barbara Materna, Acting Chief, Occupational Health Branch, CA Dept. of Health Services Appendix B: Letter from Barbar Materna to Steve Skurna, President of Micro Metallics Appendix C: Report: Occupational Health Branch Walk Through of Micro Metallics I. EXECUTIVE SUMMARY The problem of electronic waste (e-waste) is growing at an unsustainable rate. E-waste is now the fastest growing, and most toxic, component of municipal garbage. Local governments are facing huge costs to handle e-waste, and even greater costs if they do not capture this toxic stream and handle it in an appropriate manner. Recycling is both a means of preventing the land disposal of toxic metals in e-waste and recovering some value. The Computer TakeBack Campaign, an advocacy coalition, is developing and campaigning for appropriate models for managing e-waste. (For more information about the campaign, its goals and work see http://www.computertakeback.com). This case study compares two very different models for recycling obsolete computers and electronics hardware that have been created by the two largest computer makers in the U.S. — Hewlett Packard’s partnership with Micro Metallics of Roseville, California, and Dell Computers’ (recently renamed Dell, Inc.) partnership with UNICOR, the Federal Prison Industry. Our methodology included visits to both sites to examine the facilities for a number of characteristics: • Transparency and accountability to the public Handling large amounts of e-waste poses risks of toxic contamination to workers and surrounding communities if conducted carelessly. Thus, the most basic criterion that employees and citizens should rightfully expect from any recycling operation is that it be open to public inspection. • General compliance with occupational health and safety standards Observance of health and safety standards in the workplace is important for protecting workers from exposure to toxics. It is also a powerful indicator of broader compliance with environmental requirements. Well-trained workers, who are fully protected by the law to seek advice and take action to protect their health and the environment without fear of reprisal from their employer, are the most effective environmental protection. Operations that expose workers to hazards also frequently fail to protect communities around their facilities from dangerous emissions. Seldom does an industrial facility with a well-managed occupational health and safety program, and workers who are fully empowered to initiate corrective actions, violate environmental standards. • Use of best recycling practices and their potential for wide adoption by the private sector Electronic waste is a fairly new category of resource recovery. As the nation responds to this growing challenge to waste management systems and the environment, we must quickly develop the infrastructure required to handle huge volumes of e-waste. How do we build this new segment of our economy so that it is thriving, sustainable and independent of the public treasury? This study found that the two facilities differed dramatically in their transparency to the public. The Atwater facility exhibited a “fortress UNICOR” mentality, allowing only restricted access to investigators. UNICOR failed to respond to repeated requests to allow an industrial hygienist trained in occupational health and safety to inspect its facility, approving the visit too late for its findings to be included here. During a visit by other inspectors for this study, both investigators and inmates were forbidden from speaking with each other. Fortunately, the investigators were able to supplement their observations with testimonials from inmates, which are presented anonymously in this report to protect prisoners from reprisal. The Atwater facility refused to provide air quality test results, claiming that this information would have to be sought through a Freedom of Information Act request addressed to the federal Bureau of Prisons. “Even when I wear the paper mask, I blow out black mu- In contrast, the Micro Metallics - Hewlett-Packard facility allowed our industrial cus from my hygienist to inspect freely, permitted investigators to speak informally with employnose everyday.” ees, and provided air monitoring and employee blood –lead test results. ---an inmate at Atwater The strikingly dissimilar picture at the two operations offers a contrast between some of the worst and best recycling practices. Safety and health standards were very different at the two recycling operations. At Atwater, UNICOR’s primitive practice of manually smashing leaded glass in cathode ray tubes unnecessarily exposed workers to risk of toxic contamination and cuts. Security restrictions on the kinds of tools available to prisoners made their work less efficient and more dangerous. Workstations were not designed to avoid ergonomic hazards. One inmate reported that “Even when I wear the paper mask, I blow out black mucus from my nose everyday. The black particles in my nose and throat look as if I am a heavy smoker. Cuts and abrasions happen all the time. Of these the open wounds are exposed to the dirt and dust and many do not heal as quickly as normal wounds.” Inmates reported that those who sought to improve conditions faced discipline and loss of their jobs. At Micro Metallics – HP, hazardous tools such as hammers were eliminated in favor of mechanized systems, such as crushers, that reduce worker exposure to toxics. The facility’s workstations were designed to reduce ergonomic hazards. An intranet database allowed workers to access information on hazardous materials and optimal methods for safe disassembly. The strikingly dissimilar picture at the two operations offers a contrast between some of the worst and best recycling practices. UNICOR’s operation is organized primarily to maintain a maximum-security facility, rather than to maximize the efficiency with which e-waste is sorted and disassembled. Its prison warehouse is organizationally and technologically backward. Cheap labor, paid .20 to $1.26 per hour at Atwater, offers little incentive to invest in worker productivity. In addition, prison workers have few rights and little ability to improve health and safety conditions. Inmates toil outside the protection of state and local environmental and labor regulations that private sector recyclers must follow. Prison laborers are not considered employees and are not protected against retaliatory acts by their employer (UNICOR) under the Fair Labor Standard Act. Inmates are not allowed to unionize or to serve on the prison health and safety committees. In contrast, Micro Metallics – HP had developed efficient warehousing systems that electronically track materials throughout the recycling process. The facility was staffed UNICOR, a by union workers paid a living wage. Non-management employees sat on the company’s publicly subsi- health and safety committee. They helped create a workplace that was open to public inquiry and able to respond to state and local regulatory agencies. dized prison industrial operator, used practices disturbingly similar to those found in developing nations. UNICOR, a publicly subsidized prison industrial operator, used practices disturbingly similar to those found in developing nations, which were exposed in the 2002 report, Exporting Harm http://www.svtc.org/cleancc/pubs/technotrash.htm. Inspectors found harsh conditions, very few worker rights and protections that are guaranteed to hazardous waste recycling workers in the US, and lack of disclosure of its practices to the public. The Micro Metallics – HP facility, a private sector operation, had much higher levels of demonstrable health and safety and environmental safeguards. In addition, while Hewlett-Packard has committed to a policy of not exporting hazardous ewaste to developing countries, UNICOR has acknowledged that e-waste processed in their facilities is likely exported overseas to foreign countries for final disposition. Because of the lack of transparency surrounding the UNICOR facility, its inefficient and unnecessarily dangerous recycling practices, and the undetermined taxpayer subsidy that underpins its operation, planners and policy makers will be able to learn much from their operations about how not to set up a sound e-waste recycling program. The Micro Metallics facility, while not yet offering comprehensive solutions, offers a far better model for further study and imitation. These recycling operations suggest two paths for the future of e-waste recyE-waste recy- cling in America. One path leads toward efficient, transparent, modern facilities staffed cling can con- by free labor, possessed of their rights as contemporary employees, able to protect tribute to com- themselves and nearby communities from harm. The other path descends into a closed, Dickensian world of prisoners condemned to dangerous work for little pay under backmunity eco- ward conditions. Depending on the path we choose, e-waste recycling can contribute nomic develop- to community economic development and environmental protection, or can become the ment and envi- equivalent of breaking rocks on a high-tech chain gang. ronmental protection, or can become the equivalent of breaking rocks on a high-tech chain gang II. INTRODUCTION A. Background ute to the local economy without taxpayer subsidy, and which do not create health or environmental problems. Consumer electronics, especially computers and televisions, contain more than 700 different types of materials, most of which are hazardous.1 (See Section B: Hazardous Materials in E-Waste and their Effects on Humans and the Environment.) Computer monitors, televisions and several consumer electronic devices (CED) are banned from landfills in California and Massachusetts, and more than one-half of the states in the U.S. have introduced legislation to adThe problem of electronic waste (e-waste) is growing dress hazardous e-waste. Although consumer elecat an unsustainable rate. E-waste is now the fastest tronics contain some valuable metals, chips, and parts, growing, and most toxic, component of municipal gar- these constituent materials are difficult and time-conbage. Local governments are facing huge costs to suming to recover due to poor product design. Since handle e-waste, and even greater costs if they do not these poorly designed products require cheap labor capture this toxic stream and handle it in an appropri- to perform manual disassembly most waste is currently shipped overseas to Asian countries or sent to US ate manner. prisons for “recycling.” Recycling is both a means of preventing the land disposal of toxic metals in e-wastes and recover- An earlier investigation by two of CTBC’s member ing some value. The Computer TakeBack Cam- organizations, the Basel Action Network (BAN) and paign, an advocacy coalition, seeks appropriate models Silicon Valley Toxics Coalition (SVTC), documented what happens to computers and electronic devices for managing e-waste. dismantled in China. BAN investigators documented The purpose of this case study is to examine two dif- women and children using crude tools, dangerous ferent models for end-of-life disposition employed by chemicals, and open pit fires to recover precious metthe two largest US computer manufacturers who mar- als, copper, and chips. ket “recycling” of e-waste to their customers. SVTC visited the recycling facilities of Micro Metallics, The widely distributed report, Exporting Harm: Hewlett Packard’s recycling partner, located in The High-Tech Trashing of Asia, significantly Roseville California and the United States Penitentiary increased awareness among recyclers, and many in Atwater, Dell Inc’s recycling partner, to compare have publicly pledged to stop shipping waste overthe recycling systems of the two largest US computer seas.2 Ending this export to developing countries, makers. lacking both worker and environmental protections and a transparent and democratic infrastructure for overThus this initial CTBC report focuses on Atwater sight and enforcement requires an ongoing, consistent, Prison and Micro Metallics health and safety issues and economically stable network of recyclers in the relating to worker rights, the recycling disassembly US. Many companies in the U.S. – including Hewlett processes, and materials processing mechanism. From Packard and Dell — have responded to this report this comparison, we intended to learn what character- by pledging that they will not export e-waste to develistics waste managers and policy decision makers might oping countries. Dell spokesperson Cathy Hargett emulate as they began to develop their own programs. told The Oregonian newspaper in an article that apOf special concern is the need for ongoing programs peared on April 18, 2002: “Dell has a no-landfill, nothat are economically sound and stable, that contrib- export policy. All of our recyclers have to meet that.” The Computer TakeBack Campaign (CTBC) was formed to promote clean design and brand owner responsibility for discarded computers and electronics. The principle of producer take-back shifts the burden for collection and recycling costs off of taxpayers and government to the producers, providing an incentive for companies to market products that are durable, less-toxic, and recyclable. Section III outlines the method of inquiry used by SVTC during our visits to the two recycling facilities. This section also provides an overview of the disassembly and materials processing and how these activities correlate with health and safety issues. In genA spokesman for UNICOR confirmed that UNICOR eral, we use this test as a proxy for environmental comdoes in fact sell the waste to companies which more pliance as well. An industrial facility with a well-managed occupational health and safety program will usuthan likely export it. ally also have high environmental standards. On the “It’s absolutely possible the stuff ends up other hand, operations that routinely expose workers to hazards frequently have poor pollution control/prein other countries,” he said. “But we don’t vention measures at their facilities. Well-trained workreally see the problem with that.” 3 ers, who are fully protected by the law to seek advice and take action to protect their health and the environment without fear of reprisal from their employer, Environmental health and safety issues in the electronic are the mot effective environmental protection. Workrecycling industry are clearly broad and complex. This ers are like the “canaries in the coal mine” and can be is an initial investigation that examines two differ- the early warning system when they become ill from ent models of partnerships structured by computer exposure to hazardous materials. companies for end- of-life management of their products. These evaluations of the strategies em- When we can observe impacts or threats ployed by HP and Dell Inc will form the basis for to their health and safety, we should exfuture research and action by the CTBC. Dell’s use of UNICOR raises doubts about this claim, however. UNICOR’s “lack of transparency” means the e-waste could be sold to other companies, which then export the waste. UNICOR will not disclose who buys the material. pect to find more extensive environmental Electronics recycling is at a critical juncture in its de- impacts as well. velopment. OEMs are in a position to make a choice of investing in the development of prototype factories and financing R &D projects that will develop equipment and systems that protect human health and the environment and build economic benefits in the US. Alternatively, they can continue to seek cheap labor and lax worker and environmental practices, through the practice of sending hazardous e-waste to Asian villages or to U.S. prisons. How this choice is made by multi-billion dollar U.S. computer companies – the high road vs. the low road — will determine to a significant degree the future of computer recycling in the United States. B. Report Structure This document outlines the findings of the SVTC staff visits to the two recycling facilities. The report emphasizes issues relating to workers rights, recycling disassembly processes, materials processing mechanism and is organized in the following way: Section IV provides an overview of SVTC observations during the tour of both facilities. Because SVTC staff was not afforded the opportunity to speak with prisoners, this preliminary document supplements what we saw at the prison facility with letters written to SVTC by inmates from US Penitentiary Atwater. III. OVERVIEW A. Health impacts of Hazardous Electronic Waste Electronic recycling is an emerging industry with limited technology, systems or standards. Although consumer electronics contain some valuable metals, chips, and parts, these constituent materials are difficult and timeconsuming to recover due to poor product design. Currently these poorly designed products require cheap labor to perform manual disassembly. The UNICOR recycling program’s goal is to put as many prisoners to work as possible, resulting in the use of manual labor rather than mechanization. The impacts of the recycling and dismantling operations on worker health, generally has not been well-studied, and thus the impacts of specific operations on worker health remain poorly understood. What is known is that the potential for seriously adverse effects is a cause for great concern. These concerns were unfortunately confirmed in the Chinese villages where workers suffer chronic illness such as skin rashes and respiratory problems and where the residents cannot drink the water because of acute contamination. Workers in electronics demanufacturing and cathode ray tube recycling (CRT) operations are exposed to a variety of heavy metals during processing, such as lead and cadmium. In addition, they are exposed to brominated flame retardants from handled and shredded plastics, and undergo ergonomic strains and stress from manual lifting and operating hand equipment and long term hearing loss related to the operation of heavy equipment. 4 Research reveals that people working at an electronics dismantling plant showed significantly higher levels of all brominated flame retardants in their blood serum as compared to a control group.5 In addition, a recent study of occupational health risk associated with electronic demanufacturing showed higher levels of lead and cadmium at workstations that manually break CRTs found inside computer monitors and televisions, as is performed in prison, than workstations that mechanically cut CRT glass.6 Computer monitors and televisions contain lead, cadmium, mercury switches, polyvinyl chloride, brominated flame-retardants, phosphates, beryllium and a host of other hazardous materials and are banned from landfills in California, Minnesota and Massachusetts. More than one-half of the states throughout the U.S. have introduced legislation regarding end-of-life management of hazardous electronic equipment. B. Hazardous Materials in E-Waste and their Effects on Humans and the Environment Lead 7 Lead is known to cause damage to the central and peripheral nervous systems, blood system and kidneys in humans. Effects on the endocrine system have also been observed and its serious negative effects on children’s brain development have been well documented. Lead accumulates in the environment and has high acute and chronic toxic effects on plants, animals and microorganisms8 . Consumer electronics constitute 40% of lead found in landfills. Cadmium 9 Cadmium compounds are classified as toxic with a possible risk of irreversible effects on human health. Cadmium and cadmium compounds accumulate in the human body, in particular in kidneys. Cadmium is adsorbed through respiration but is also taken up with food. Cadmium shows a danger of cumulative effects in the environment due to its acute and chronic toxicity10 . Mercury 11 When inorganic mercury spreads out in the water, it is transformed to methylated mercury in the bottom sediments. Methylated mercury easily accumulates in living organisms and concentrates through the food chain particularly via fish. Methylated mercury causes chronic damage to the brain. It is estimated that 22 % of the yearly world consumption of mercury is used in electrical and electronic equipment. It is basically used in thermostats, (position) sensors, relays and switches (e.g. on printed circuit boards and in measuring equipment) and discharge lamps, batteries, switches/housing, medical equipment. Hexavalent Chromium (Chromium VI)12 Some manufacturers still apply this substance as corrosion protection of untreated and galvanized steel plates and as a decorative and hardener for steel housing.Chromium VI can easily pass through membranes of cells and is easily absorbed producing various toxic effects within the cells. It causes strong allergic reactions even in small concentrations. Asthmatic bronchitis is another allergic reaction linked to chromium VI. Chromium VI may also cause DNA damage. Brominated Flame Retardants Brominated flame-retardants are a class of brominated chemicals commonly used in electronic products as a means for reducing flammability. Various scientific observations indicate that Polybrominated Diphenylethers (PBDE) might act as endocrine disrupters. Researchers in the US found exposure to Polybrominated Biphenyls (PBBs) may cause an increased risk of cancer of the digestive and lymph systems. C. Methodology Electronics recycling is at a critical juncture in its development. OEMs are in a position to make a choice of investing in the development of prototype factories and financing R &D projects that will develop equipment and systems that protect human health and the environment and build economic benefits in the US. Alternatively, they can continue to seek cheap labor and lax worker and environmental practices, through the practice of sending hazardous e-waste to Asian villages or to U.S. prisons. How this choice is made by multi-billion dollar U.S. computer companies – the high road vs. the low road — will determine to a significant degree the future of computer recycling in the United States. During SVTC visits we focused on the following: - Disassembly process Development of efficient materials processing systems Worker protections SVTC selected the Micro Metallics facility located in Roseville California and the US Penitentiary in Atwater because they represent approaches to end-of-life management taken by the two largest US computer makers. Dell Computers, with $31.1 billion revenue in 2002,13 has a partnership with UNICOR, the not-for-profit business branch of the Federal Bureau of Prisons. UNICOR earned $116.8 million in electronics recycling sales in 2001 and employed 3,269 inmates at its 13 electronic recycling factories.14 The total number of UNICOR electronic recycling facilities in 2003 has been consolidated to six facilities, according to UNICOR officials. Hewlett Packard, which reported $72.3 billion revenue in 2002,15 entered into a joint venture with Micro Metallics in 1996 to recycle materials recovered internally and to recover parts from products returned by customers. The Roseville facility has since expanded to process some computers returned through the HP customer Product Return & Recycling Program. A similar facility has been built in Tennessee. When the $5 million Roseville recycling plant opened, it helped to set a US benchmark for other OEMs for their extended producer recovery programs. OEMs, such as Dell and HP, recycle thousands of tons of computers and peripherals annually, and thus already have incredible influence over how the recycling infrastructure evolves in local communities. In the future, OEMs, by their contracting decisions, will largely control how and under what circumstances their materials are recycled. The goal of this initial inquiry is to examine health and safety issues relating to workers rights, the recycling disassembly processes, and materials processing mechanism. (Subsequent CTBC reports will compare the economic impact of prison labor against the private sector to examine local community development benefits). 1. Overview of Electronic Disassembly, Recycling Processing and Workers Health and Safety Protections 1A. Disassembly Process According to experts, disassembly is the first and most important point in the recycling process, and it will be a key component of the recycling industry’s rate of expansion. Disassembly requires the removal of plastic housing and the recovery of toxic components and often entails the recovery of metals, chips, and parts for reuse. While engineered for efficient assembly-line production, electronic products generally have not been designed for efficient disassembly-line dismantling. Products received by recycling facilities are not uniform and represent diverse product brand names, models, and years. Currently, disassembly for recycling, if performed at all, relies heavily on manual labor. But with the enormous increase in products to be recycled and therefore to be disassembled, it will increasingly be necessary to automate some aspects of disassembly. High flexibility and low-cost of disassembly process are becoming more necessary. The automation potential will be one of the most important productivity factors for this new production process and becomes a new challenge for engineers as well as product designers. According to industry experts, the two main goals of disassembly should be the following: • • Reduce the cost of disassembly for optimizing the recycling process Create a humane working environment in disassembly factories16 Although some OEMs have invested in facilities to test or demonstrate disassembly systems, there is very little feedback from recyclers to OEMs on the disassembly process, compared to the type of communication that exist between a company such as Dell or HP and the contractors who assemble their products for delivery to market. In order to create a sustainable and profitable recycling system that doesn’t require OEMs to rely solely on finding the cheapest labor pools and laxest environmental standards, OEMs will have to invest in systems, tools, technology and equipment that reduces worker exposure to toxics, increases the speed in which products are disassembled, and the speed and safety which toxic components such as mercury switches and batteries are removed and constituent materials processed. During our visits to the US Penitentiary in Atwater and the Micro Metallics facilities, the SVTC investigators observed the tools that disassemblers used and the design of the workstations. 1.B. Development of efficient materials processing systems The constituent metals, glass, and plastics found in electronics are generally low value. The glass cathode ray tubes (CRT) found in televisions and computer monitors contain lead in order to protect the user from radiation from the cathode “rays”. Because the lead is so hazardous, CRT glass must be smelted or sent to a glass-to-glass recycler that can recycle it into new products. Glass-to-glass recycling refers to the closed loop recycling process of reclaiming leaded CRT glass from end-of-life CRTs and using it to make new CRT glass. Glass-to-glass recycling involves collecting televisions and monitors, removing and crushing the CRTs, separating the glass from the non-glass materials, processing the glass to meet specifications, and using the glass as an ingredient to manufacture new CRT glass. According to the Electronics Industry Alliance, “There is no available technology that provides an effective and economical method for CRT glass manufacturers to determine the composition of recycled glass. Therefore, due to the potential risk of adding recycled glass with the wrong composition, CRT glass manufacturers have limited capacity to increase the use of recycled glass in lieu of raw materials to manufacture new CRT glass.”17 Because CRT manufacturers have not developed technology that makes glass separation economically feasible, recyclers often cut their costs by using cheap labor in developing regions of the world such as the Guangdong Province of China (as documented in “Exporting Harm”), Pakistan, India, and Thailand or— as in one of the cases studied in this report— the US prison system. The other alternative is to reduce the human handling of the CRTs by purchasing a shredder that mechanically grinds and separates constituent materials. However, the output streams from the shredders are a relatively low value mix of plastic, glass, and metals that cannot be used in a glass-to-glass process. Although just about every household in the US has a television and/or a computer monitor bearing a CRT, OEMs and their contractors have not yet invested in developing systems that combine the necessary manual or automated disassembly with mechanical shredding processes. 1C. Worker and Environmental Protections Workers who process hazardous waste should have unencumbered freedom and access to information and advice about hazardous materials and should have full protections under the law. Hazardous waste workers should also have the ability to take action to protect their health and the environment without fear of reprisal. For the purpose of this report, SVTC primarily focused on environmental health and safety issues related to worker protections. In general, we use this test as a proxy for environmental compliance as well. Well-trained workers, who are fully protected by the law to seek advice and take action to protect their health and the environment without fear of reprisal from their employer, are the mot effective environmental protection. Rarely does an industrial facility with a well-managed occupational health and safety program also violate environmental standards, while operations exposing workers to hazards frequently find it difficult to stop their hazardous emissions from exiting their facilities. Well-trained, well-protected workers have always been the first and most effective environmental protection. They serve as our “canaries in the coal mine.” When worker health and safety is compromised, experience teaches us that we should also expect environmental problems. When workers cannot speak about the hazards they observe, either because of the lack of basic training or because of the lack of workplace rights and protection – and the related fear of reprisals — the public is likely to discover extensive problems only after a disaster or scandal. Prisons are self-contained communities designed to isolate inmates from social life. They deny inmates of some of the most basic rights and privileges of the law. Federal prisons are also not effectively regulated by many local state and federal environmental and labor laws. These are not ideal circumstances to process hazardous waste. Concerns about workers health and safety protections and the transparency of the prison system were heightened when the federal prison officials denied our request that we bring an occupational health expert with us. We had formally requested to prison officials that Dr. Barbara Materna, Acting Chief of the Occupational Health Branch of the California Department of Health Services (DHS) be allowed to join us on our tour. In spite of our many requests, Dr. Materna was not allowed to accompany SVTC staff on the tour of the Atwater Prison Facility, nor were we provided opportunity to speak with any of the prisoners during our visit. On the other hand, HP - Micro Metallics welcomed Dr. Materna to its Roseville facility and treated her visit rather routinely. Due to the inaccessibility of interviews with the prisoners, this preliminary report supplements what we observed at the prison with what inmates described in their letters.18 The Occupational Health Branch of DHS is a non-regulatory public health program, which conducts research and public education about occupational disease and injury among California workers. Dr. Materna, an expert in occupational lead poisoning prevention, expressed interest in assisting SVTC to learn more about the electronic recycling industry and worker health and safety issues. Electronics recycling is a relatively new industry and the potential environmental health impacts due to chemical exposures are relatively unknown and undocumented. Materna and the Occupational Health Branch of DHS need to be among the specialists providing leadership in research on the persistent bio-accumulative toxins released through the electronics recycling process. As a standard procedure, Dr. Materna initially visits a facility, observes and discusses health and safety measures with management and staff, and makes recommendations. Dr. Materna was able to talk with HP-Micro Metallics’ staff and to make an initial report (See Appendix A). IV. SVTC TOUR OF RECYCLING FACILITIES A. Visit to Micro Metallics 19 1. HP - Micro Metallics Recycling Warehousing System The Micro Metallics recycling facility was built in 1996 to recover and reuse HP’s products and to test recycling methods. The factory is designed to recover usable parts, move the materials through the warehouse as efficiently and with as little labor as possible. Each pallet of electronic waste is labeled with a source customer code (SCC) upon entering the facility. The SCC, which resembles a bar code, also provides information to the workers about the hazardous materials contained in the electronic waste and if there are any valuable parts to salvage. The SCC also allows HP Micro Metallics employees to electronically track the materials throughout the warehouse and to eventually inform HP and other clients of how the recycled materials were processed, if there is any value in the material, and who are the down-stream vendors of the recycled materials. 2. HP - Micro Metallics Disassembly Process The Micro Metallics disassembly workstations are well-lit, ergonomically designed, and computerized. Each workbench is equipped with a hand-held device to scan the SCC and retrieve information about the equipment to be salvaged. If a worker is unfamiliar with a piece of equipment they can log onto the HP - Micro Metallics computer intranet and conduct a search for information about the equipment design or find-out if the equipment contains any hazardous components. Other features of the workstation include tabletops that can be raised or lowered from 24" to 48" to avoid back injury and several of the tables are equipped with hydraulic lifts for dismantling heavier items. The workers sit on 5-wheel chairs that can be raised and lowered to a height comfortable to the worker. Motorized pallet jackets and forklifts are also used to avoid worker injury. Tools are assigned for specific tasks and air driven tools are used to reduce the use of hand operations. Screwdrivers are used as a last resort. Workers are encouraged to provide feedback on product design and to suggest alternative tools to improve safety and efficiency. For example, hammers were determined to be too dangerous and banned from the disassemblers’ tool kit. All brooms have also been removed from the facility and replaced with vacuum cleaners in order to keep the dust under control. Sweeping is thought to stir up fine dust particles that could contain lead, brominated flame retardants, and other toxins from the computer dismantling and shredding operations. 3. Micro Metallics Materials Processing System Micro Metallics workers send non-reusable computers through their mechanical shredder, which grinds and separates materials using eddy currents, magnets and screens. The resulting output stream is sent to Noranda’s smelter in Quebec, Canada, or sold to recyclers approved by Micro Metallics and its clients. HP also contracts with private sector recyclers, which they say they audit. HP does not use prison labor in any of its operations. 4. Micro Metallics Worker Protections 4.A. Health and Safety Program Dr. Materna participated in a walkthrough of the HP-Micro Metallics facility in response to a request from SVTC to provide industrial hygiene expertise as part of an overall effort to better understand the potential worker health and safety risks associated with computer/electronics recycling. Dr Materna provided a brief report of the process, potential health and safety hazards, and health and safety program based on her direct observations during the walkthrough, informal discussion with employees, conversations with several Micro Metallics personnel, including Mr. John Quinn, EH&S Manager and a follow-up discussion and follow-up phone call with the Chief Shop Steward. Dr. Materna expressed concerns were in the area of ergonomics, which she considered to be one of the more significant potential hazards at the HP-Micro Metallics facility. As a follow-up Dr Materna suggested airdriven tools be suspended from above the workstation in order to decrease ergonomic stress and Dr. Materna felt that these concerns were being addressed. Air monitoring data and blood-lead test of the Micro Metallics workers were provided to Dr. Materna by Micro Metallics, per the request of SVTC. (See Dr. Materna Report in Appendix A.) 4.B. Worker-Initiated Protections The workers are members of the International Association of Machinists and Aerospace Workers Union, earn from $8-$13 per hour and receive full health benefits. All Federal, state, and local rules and regulations apply to the Micro Metallics facility. Workers who report occupational and environmental hazards are thus protected by Federal whistleblower laws as well as by union contract provisions. B. Visit to United States Penitentiary in Atwater UNICOR Recycling Facility20 1. UNICOR Warehousing System Arriving e-waste is first searched when it arrives at the “camp” warehouse facility located on the outer perimeter of the main prison. The e-waste will be searched 3-4 more times as it goes through the recycling process at the prison facility. The approximately 40 inmates who work in the camp are considered low risk and recycle a broad range of materials including typewriters and Department of Defense equipment. The computer monitors and televisions are restacked and sent behind the “fence” to the main facility. Once inside the main facility the materials are unpacked and searched again before they are distributed to higher risk inmates for dismantling. The hazardous e-waste is disassembled and separated into plastic housing, metals and CRT and other constituent materials by approximately 275 inmates. The materials are unpacked, searched and re-packed at least 2-3 more times before leaving the prison facility. The number of times the materials are packed and unpacked for security purposes would be considered extremely counter-productive to most warehouse operations, which attempt to reduce labor costs by reducing the number of times the materials are handled by workers. Furthermore, the extra handling steps add to potentially harmful exposure. In comparison to the tracking and warehousing system observed at HP-Micro Metallics, the US Penitentiary at Atwater system is thus highly inefficient, necessitates more exposure time to the hazardous components of e-waste, and increases risks. 2. UNICOR Disassembly System Security is the primary concern of the prison. The US Penitentiary at Atwater recycling operation is organized around the principal goal of maintaining a maximum-security facility, rather than maximizing the efficiency with which e-waste is disassembled. The 240 prisoners who work dismantling televisions, computers, and other electronic equipment sit in an assortment of plastic and common folding chairs at long makeshift tables. The workstations are not ergonomically designed to reduce work related injuries. The tools used for disassembly in the prison are selected largely on whether or not the tools pose a security risk. Consequently, inmates often have to use tools that aren’t suitable to the tasks and that can cause injury. Larry Novicky, who heads up the UNICOR recycling services division, stated in a letter to SVTC that “the use of hammers in a recycling operation is a basic industry fact that is standard for many various activities21 .” However, as noted previously, HP-Micro Metallics has banned hammers from their operation due to concerns about the dangers of shattered glass and plastic shards. Security restrictions on the types of tools that can be given to inmates sometimes require inmates to resort to using a hammer as their primary tool for disassembly.22 An inmate explained in a letter to SVTC how he and others are often cut by glass shards from CRTs due to the lack of appropriate drill bits and other tools. “…the sinkholes in the television or monitor plastic housing are frequently deeper than the length of the drill bit. Thus we are give (sic) woefully inadequate-sized bits to get at the deeper screws. To get around this problem, inmates must hit the case with the hammer in the general area of where the screw holds the case to the inner screw stanchions or misuse the air gun to drill the plastic away from the screw stanchion to free the case. The orderlies/janitors sweep the tabletops and floors which also stirs-up additional dirt and dust for all to breath. Even when I wear the paper mask, I blow out black mucus from my nose everyday. The black particles in my nose and throat look as if I am a heavy smoker. Cuts and abrasions happen all the time. Of these the open wounds are exposed to the dirt and dust and many do not heal as quickly as normal wounds.”23 3. UNICOR Materials Processing System Another example of the misuse of hammers is in the prison CRT crushing room. The CRT is the glass tube found inside television and computer monitors. CRTs contain leaded and barium impregnated glass and the phosphor compounds inside the tubes can be easily inhaled without due care. SVTC staff expected to see a closed-system mechanical crushing machine housed inside a secured room. To our surprise, the crushing consisted of 8-12 inmates in a caged area blocked with strips of plastic sheeting, smashing CRTs with a hammer. The inmates wore haz-mat suits, respirators, and the room was equipped with a filtration system. We requested monitoring test results of the workplace air because of our concern that unnecessary and dangerous levels of phosphor and glass dust and possibly lead and barium compounds could be present. Recent studies of demanufacturing work areas show a migration of lead into non-work areas, including break rooms and washrooms. The concentration of lead may be minimal, but its accumulation over time in areas where there is a greater risk of exposure through ingestion is a concern.24 However, requests made by SVTC, for air moni- toring test results have been denied by UNICOR25 . SVTC was told we would have to seek the information from the Bureau of Prisons, not through normal public information processes, but under provisions of the federal Freedom of Information Act.26 Micro Metallics, however, freely provided air monitoring test results as well as worker blood test results to DHS researchers. Smashing CRTs with hammers is not a common practice in the private sector, nor could it ever be considered a “best practice.” A recent study of occupational health risk associated with electronic demanufacturing showed higher levels of lead and cadmium at workstations that manually break CRT glass than workstations that mechanically cut CRT glass.27 The crude method of crushing and separating the glass is considered too dangerous and costly by most private sector recyclers. The CRT glass is of extremely low value, and most private sector recyclers could not afford to employ 8-12 workers to don hazardous material suits and use hammers to manually crush CRTs for 8 hours a day. In fact, many recyclers throughout California are seeking capital investments to install self-contained mechanical crushers similar to the one used by HP-Micro Metallics. UNICOR’s practice of using hammers to smash leaded CRT glass more closely resembles the labor-intensive CRT processing observed by BAN in Guangdong Province, China than regulated private sector operations in the US. 4. UNICOR Worker Right and Health and Safety 4A. Health and Safety Program Dr. Materna was not allowed to participate in a walkthrough of the US Penitentiary at Atwater facility. Thus SVTC and the general public were not able to benefit from Dr Materna’s observations, or recommendations for the purpose of this report (See Appendix B). Unlike the tour of Micro Metallics in which Dr Materna and SVTC were allowed to informally speak with employees, SVTC was forbidden to speak with prisoners while on the tour and, and the inspection group was not provided an opportunity to speak with prison workers in a formal interview. Prisoners are not allowed to unionize and therefore do not have a shop steward in which to follow-up. Prisoners are not allowed a representative on the Prison Health and Safety Committee to represent their views or advocate their concerns. As mentioned above, requests made by SVTC, for air monitoring test results have been denied by UNICOR. SVTC was told to seek the information from the Bureau of Prisons, not through normal public information processes, but under provisions of the federal Freedom of Information Act. 4B. Worker-Initiated Protections Many of the federal, state and local environmental and labor regulations that private sector recyclers must follow don’t apply to the federal prison system. For example, the Whistle Blower Protection Action of 1989 does not apply to inmates.28 The Act is designed to protect the so-called “whistleblower,” an employee who believes that he or she has been discriminated against from retaliatory or discriminatory action by their employers subsequent to informing regulatory enforcers about abuses and unsafe practices. However, inmates are not considered employees and are not protected against retaliatory acts by their employer (UNICOR) under the Fair Labor Standard Act.29 Inmates at UNICOR’s Atwater Prison recycling factory earn $0.20 to $1.26 per hour and are not allowed to form a union. Several prisoners incarcerated at Atwater who work in the electronic recycling factory have written to SVTC expressing concern about health and safety conditions and seeking information about the hazardous materials contained in the computers. Inmates write that disciplinary action is taken against those who report violations, try to bring about changes in safety procedures, make recommendations for better tools or request more training. Inmates also said that they were warned not to speak with SVTC when we toured the facility or they would “suffer disciplinary action or loss of job.”30 Although Atwater Prison has a health and safety committee that oversees all of the facility’s activities, unlike the HP-Micro Metallics committee, it does not have a health and safety committee that specifically oversees the electronics recycling operations. Nor are inmates (non-management) personnel represented on the health and safety committee as they are at the HP-Micro Metallics facility. Therefore the concerns of the 275 inmates are not adequately represented on the health and safety committee. Instead, inmates are required to submit written complaints to their supervisor. The supervisor is required to respond to the he complaint within 72 hours. However, prisoners claim that health and safety complaints to the supervisors are often met with reprisal from the supervisor.31 IV. CONCLUSION_______________________________________________________ This case study compares two very different models for recycling obsolescent computers and electronics hardware that have been created by the two largest computer makers in the U.S. — Hewlett Packard’s partnership with Micro Metallics of Roseville, California, and Dell Computer (recently renamed Dell, Inc.) partnership with UNICOR, the Federal Prison Industry. Our methodology included visits to both sites to examine the facilities for general compliance with worker protections and occupational health and safety standards and use of best recycling practices. We found that of the two systems, HP –Micro Metallics partnership provided the best model for worker health and safety protection. The HP-Micro Metallics facility demonstrated characteristics that other electronic waste managers and policy decision makers might emulate as they begin to develop recycling programs. Alternatively, the Dell, Inc.’s choice of the US prison system lacks a commitment to invest in a socially and economically sustainable infrastructure. The prison system’s lack of both worker and environmental protections and transparent and democratic infrastructure for oversight and enforcement more closely resembles the labor-intensive CRT processing observed by BAN in Guangdong Province, China than regulated private sector operations in the US. In her report to HP-Micro Metallics, Dr. Materna wrote that “It was a good experience to visit a work site where there appears to be a significant investment in occupational and environmental health and safety, and also mechanisms that encourage the involvement of employees in addressing health and safety issues.” Although SVTC have not observed all of the facilities in which HP equipment is recycled, the facility in Roseville California, is an industry model that sets standards for factory prototype, worker health and safety and provides examples for efficient recycling systems. The HP-Micro Metallics system sets the following standards: • • • • • • • • Eliminate tools, such as hammers, that cause injury and health hazards Hire union workers and pay a living wage Develop efficient warehousing systems that electronically track materials through recycling process Install mechanized systems, such as crushers, that reduce worker exposure to toxics Develop work stations designed to reduce ergonomic hazards Develop intranet database that allows workers to access information on hazardous materials and best methods for disassembly to avoid exposure Provide non-management representation on the company’s health and safety committee Developed transparent health and safety programs that welcome public inquiry and capable of responding to state and local regulatory agencies Alternatively, Dell Inc’s partner, the UNICOR prison program, provides a poor example of worker health and safety protections and perpetuates inefficient recycling systems in the US. Our comparison could not be completed, due to the Atwater Prison facility refusal to allow the DHS occupational health and safety expert to participate in the tour with the SVTC and their repeated denial of her requests to review the operation and make recommendations. After four months of correspondence, the UNICOR facility has recently reversed its position and has now agreed to allow Dr. Materna entry into the facility in the future. However, at the date this report was published, Dr. Materna still had not been allowed into the facility. Nor had SVTC received environmental and human health monitoring data requested from UNICOR. Thus, we found that Dell’s prison partner lacked transparency, serves as a poor model and that its workers are not fully protected by the law to seek advice and take action to protect their health and the environment without fear of reprisal from their “employer”. • Inmates are not considered employees and are not protected against retaliatory acts by their employer (UNICOR) under the Fair Labor Standard Act • Inmates earn 20 cents to 1.26 per hour • Inmates are not allowed to unionize • Inmates are not allowed representation on the health and safety committees • Prison warehousing system is inefficient and extremely counter-productive to most warehouse operations • UNICOR’s primitive practice of manually smashing leaded CRT glass unnecessarily exposes workers to toxics as well as potential injuries • UNICOR workstations are not designed to avoid ergonomic hazards • State and local environmental and labor regulations that private sector recyclers must follow frequently don’t apply to the federal prison system • Security restrictions on the types of tools that can be given to inmates leads to inefficient use of tools as well as worker injuries • UNICOR’s recycling operation is organized around the principal goal of maintaining a maximumsecurity facility, rather than maximizing the efficiency with which e-waste is disassembled ENDNOTES 1 Electronics Roadmap, 1994 Electronics Industry Environmental Road Map More than 22 recyclers have signed the Recycler’s Pledge of Stewardship developed by the Computer TakeBack Campaign. 3 Dell Computers’ recycling efforts raise labor concerns, Erika McDonald, CEC Environmental Exchange, June 2003. http://www.cechouston.org/newsletter/2003/nl_06_03/dell.html 4 Occupational Risks Associated with Electronics Demanufacturing and CRT Glass Processing Operations and the Impact of Mitigation Activities of Employee Safety and Health, Neil Peters-Michaud, John Katers, Jim Barry, IEEE International Symposium on Electronics and the Environment, 2003 5 Environmental Health Perspectives 107:643-648 (1999). [Online 29 June 1999] http://ehpnet1.niehs.nih.gov/docs/1999/ 107p643-648sjodin/abstract.html 6 Occupational Risks Associated with Electronic Demanufacturing and CRT Glass Processing Operations and the Impact of Mitigation Activities on Employee Safety and Health, Neil Peters-Michaud, John Katers, et al, IEEE International Symposium on Electronics and the Environment, 2003 7 Explanatory Memorandum, WEEE (Third Draft) July 1999, Brussels, 05.07.1999. 8 Compare Risk Reduction Monograph No. 1 Lead – Background and national experience with reducing risk, OECD Paris, 1993. 9 Explanatory Memorandum, WEEE (Third Draft) July 1999, Brussels, 05.07.1999. 10 This information is based on the risk reduction monograph no 5, CADMIUM, Background and national experience with reducing risk (OEDC/GD894) 97; Health effects of cadmium exposure – a review of the literature and a risk estimate (Lars Jarup and others) Scand J Work Environ Health 98; Environmental impacts of cadmium, Gerrit H. Vonkeman 1995; Cadmium in Sweden-environmental risks, Helena Parkman and others 1997 and other research on this issue. 11 Explanatory Memorandum, WEEE (Third Draft) July 1999, Brussels, 05.07.1999. 12 Explanatory Memorandum, WEEE (Third Draft) July 1999, Brussels, 05.07.1999. 13 http://www.dell.com/downloads/us/corporate/sec/ARFY02.pdf 14 UNICOR 2001 Annual Report 15 http://www.hp.com/hpinfo/investor/financials/annual/2002/2002text.pdf 16 Automated Disassembly of Electronic Equipment, R Knoth, M. Brandostotter, B Kipacek, IEEE International Symposium on Electronics and the Environment, 2002 17 Cathode Ray Tube Manufacturing and Recycling: Analysis of Industry Survey, Electronic Industry Alliance, Spring 2001 18 To protect the privacy of the USP Atwater inmates who corresponded with SVTC, authors of letters will be cited as John Doe followed by a letter in the alphabet. 19 March 10, 2003. Barbara Materna, DHS, Ted Smith, SVTC Executive Director, Sheila Davis, SVTC Project Director Clean Computer Campaign, visited Micro Metallics, in Roseville, CA 20 March 13, 2003. Ted Smith Executive, SVTC Executive Director, and Sheila Davis, SVTC Project Director Clean Computer Campaign, visited the recycling facility at the US Penitentiary in Atwater, CA 21 Letter to Ted Smith from Larry Novicky, General Manager, UNICOR Recycled Products and Services, March 19,2003 22 Letter received by SVTC from John Doe A. 23 John Doe A. 24 Occupational Risks Associated with Electronic Demanufacturing and CRT Glass Processing Operations and the Impact of Mitigation Activities on Employee Safety and Health, Neil Peters-Michaud, John Katers, et al 25 Email memo to SVTC Clean Computer Campaign Director, Sheila Davis, from Larry Novicky, General Manager Recycling Business Group Federal Prison Industries, 5-12-03 26 SVTC, as well as the California Department of Health Services, requested air monitoring results from the time periods before and immediately after our visit. These air-monitoring results have not been provided by the prison officials. 27 Occupational Risks Associated with Electronic Demanufacturing and CRT Glass Processing Operations and the Impact of Mitigation Activities on Employee Safety and Health, Neil Peters-Michaud, John Katers, Jim Barry, IEEE 2 International Symposium on Electronics and the Environment, 2003 28 OSHA Instruction FAP 1.2A April 10, 1995 Office of Federal Agency Programs 29 BILLIE AUSTIN BRYANT v. UNICOR/FEDERAL PRISON INDUSTRIES, Respondent, 1992 30 Letter received by SVTC from John Doe B. 31. Ibid. State of California—Health and Human Services Agency Department of Health Services DIANA M. BONTÁ, R.N., Dr. P.H. Director GRAY DAVIS Governor June 11, 2003 Mr. Stephen Skurnac President, Micro Metallics Corp. 1695 Monterey Highway San Jose, CA 95112 Dear Mr. Skurnac: Thank you for your participation in a walkthrough of the Micro Metallics Corp. computer/electronics recycling operation at your Roseville, CA, facility on March 10, 2003. My involvement in this walkthrough was in response to a request from Ted Smith of Silicon Valley Toxics Coalition, to provide industrial hygiene expertise as part of an overall effort to better understand the potential worker health and safety risks associated with computer/electronics recycling. The Occupational Health Branch (OHB) of the California Department of Health Services is a non-regulatory public health program that conducts research into the causes of work-related disease and injury, makes recommendations for improved control of workplace hazards, and provides technical assistance to employers, workers, government agencies, organizations, and individuals. Enclosed is a brief report of the process, potential health and safety hazards, and health and safety program based on my direct observations during the walkthrough and conversations with several Micro Metallics personnel, including Mr. John Quinn, EH&S Manager. Because of the brief nature of this visit, which was intended to serve as a comparison to the computer recycling operation at Atwater Federal Penitentiary, I did not request or have the opportunity to review the many health and safety records maintained by the company. I also did not conduct private interviews with plant-level employees during this visit beyond asking a few questions as we walked through the area and having a follow-up phone call with the Chief Shop Steward. Therefore, my report is limited to what I observed or discussed with a limited number of company employees. Typically, an OHB walkthrough results in our issuing recommendations for improvements to the company's health and safety program. The few concerns I had after the walkthrough were in the area of ergonomics, which I consider to be one of the more significant potential hazards. However, after discussing the topics with Mr. Quinn (e.g., controversy over the use of back belts, suggested suspension of air-driven tools from above in order to decrease ergonomic stress), I felt that these points had been considered or (in the case of the tools) already addressed. OCCUPATIONAL HEALTH BRANCH 1515 Clay Street, Ste. 1901, Oakland, CA 94612 510/622-4300 www.dhs.ca.gov/ohb Mr. Steve Skurnac June 11, 2003 Page 2 It was a good experience to visit a work site where there appears to be a significant investment in occupational and environmental health and safety, and also mechanisms that encourage the involvement of employees in addressing health and safety issues. Thank you again for your time. If you should have any questions, please do not hesitate to contact me at (510) 622-4343 or bmaterna@dhs.ca.gov. Sincerely, Barbara Materna, Ph.D., CIH Chief, Occupational Health Branch Enclosure cc: Ted Smith, Executive Director Sheila Davis Silicon Valley Toxics Coalition 760 N. First St. San Jose, CA 95112 John Quillan EH&S Manager Micro Metallics Corp. 8855 Washington Blvd. Roseville, CA 95678 James Napper Chief Shop Steward Micro Metallics Corp. 8855 Washington Blvd. Roseville, CA 95678 OHB Walkthrough at Micro Metallics Corp. June 11, 2003 Micro Metallics Corp. Computer/Electronics Recycling Operation 8855 Washington Blvd., Roseville, CA This description of the company's operation and employee health and safety program is provided by Barbara Materna, Ph.D., CIH, Chief of the Occupational Health Branch, California Department of Health Services. It is based on a walkthrough of the facility on March 10, 2003, and follow-up telephone calls with the EH&S Manager and Chief Shop Steward (the workers are represented by the International Association of Machinists and Aerospace Workers, Local Lodge 190). The visit was initiated by Silicon Valley Toxics Coalition in an effort to better understand the work process and provisions for worker health and safety for a computer recycling operation in the private sector, for comparison to a computer recycling operation in Atwater Federal Prison. Description of Process This operation, which was set up in 1996 through a partnership with Hewlett-Packard Company (H-P), receives end-of-life commercial and consumer electronic products (computers, monitors, printers, scanners, copiers) from H-P and, to a lesser extent, other customers. The equipment is tested, sorted and disassembled to recover valuable parts and remove hazardous components (batteries, ink, toner, cathode ray tubes, mercury switches, etc.) prior to recycling. The recycling process involves reducing materials to small pieces via shearing, shredding and grinding operations, and sorting the mixed material into separate recyclable commodity streams (ferrous metals, nonferrous metals with high precious metals content, aluminum-containing material, and a residual mix of plastic and nonferrous metals). The separation is done using various techniques including size-specific screens, a magnetic process, and an eddy current separator. The testing, sorting, and disassembly processes are performed by a total of 110 employees (many of them female) on two shifts. The recycling process is located in a separate section of the facility. This process is mechanized, entirely enclosed and under local exhaust ventilation with a baghouse for environmental control of dust contaminants. There is a total of twelve employees on two shifts in this department, whose jobs include mechanically emptying boxed electronic components (e.g., circuit boards, the "insides" of printers and other equipment) into the recycling operation, moving loaded boxes of separated material using forklifts, monitoring the equipment from observing video screens in a control room, and maintaining the equipment. The resulting materials that contain precious and nonferrous metals are sent to a Noranda Inc. smelter in Canada for metals recovery. There are no melting operations at this site. Other materials produced here are sent to plastics recyclers, ferrous smelters, aluminum smelters, and other facilities equipped to recycle or handle hazardous waste. Cathode ray tubes from computer monitors are sent to Envirocycle, a company in Pennsylvania that processes CRTs for reuse of the glass. Potential Health and Safety Hazards Various representatives of the company stated that the work-related injuries most often seen in this workforce include muscle strains from materials handling, carpal tunnel syndrome from disassembly operations, lacerations from sharp metal edges or (in the past) knives used in cutting tape, and injuries related to forklift operation. Based on the walkthrough, the key health and safety hazards for which control measures are needed include: 1 OHB Walkthrough at Micro Metallics Corp. • • • • • June 11, 2003 Ergonomic hazards - materials handling in both the disassembly and recycling areas; repetitive tasks and use of hand tools in disassembly Noise - in the recycling area Laceration or eye hazards - sharp metal edges; flying particles of metal/plastics in recycling area Forklifts - potential for collision with pedestrians; other contact with machinery, equipment Exposure to toxic heavy metals - when employees must perform tasks inside the recycling equipment or maintenance activities related to the baghouse (environmental control device for dusts) Description of Health and Safety Program The company's health and safety program is comprehensive and demonstrates a high level of management commitment and investment of resources. The potential hazards listed above are addressed by a combination of control measures that were either observed during the walkthrough or described by company or worker representatives. Some of the features of the health and safety program that are notable include: • High level of worker involvement - A safety committee is made up of worker representatives who meet monthly, review issues raised by employees (there is a standard form which employees can use), and make recommendations to management for health and safety improvements. The EH&S Manager is available for technical support but does not participate in decision making. All employees participate in monthly meetings where safety issues are discussed and workers provide input. • Trained staff who are dedicated to health and safety and environmental issues - This plant, which has a total of approximately 125 employees, has a full-time EH&S manager with a background in adult education and specialized training in hazardous materials management and ergonomics. Additional assistance is provided by two associates (plant-level staff) who have been provided with training in hazardous materials management, and one associate who has been provided training in industrial hygiene. • Routine inspections and air monitoring to identify and assess hazards - Monthly safety inspections are performed which include review of the use of personal protective equipment (PPE), forklift safety, emergency and other equipment, labeling, housekeeping, etc. The EH&S Manager states that he spends two hours out on the shop floor each day, observing operations on both shifts and conversing with employees. Air monitoring is conducted regularly for various contaminants (e.g., lead, cadmium, beryllium, chromium) and job tasks. • Continuous employee training - The company has a full program for employee training on topics such as ergonomics, lockout/tagout, respirators, forklifts, hearing conservation, hazard recognition, and hazard communication. EH&S staff receive training to increase their EH&S knowledge and skills, and be able to provide training to employees on health and safety topics. There is a trained emergency response team to address first aid, spills, and emergencies, and also a program for on-the-job training in proper use of tools and equipment. • Use of appropriate engineering and work practice controls - The fact that the recycling operation is automated, enclosed, and ventilated, greatly reduces risks associated with materials handling and exposure to toxic contaminants. During the walkthrough, various 2 OHB Walkthrough at Micro Metallics Corp. June 11, 2003 types of equipment that reduce ergonomic hazards and risk of injury were observed, including air-actuated hand tools (e.g., to reduce the force needed to remove screws) and mechanized lifting devices. To minimize exposure to dust, brooms have been replaced with rubber squeegees or rakes and HEPA vacuum units. • Use of appropriate personal protective equipment - There is a respirator program that covers the use of full-face respirators which are worn by employees who have to access or enter the recycling operation or perform maintenance on the baghouse. Other types of PPE observed during the walkthrough include hearing protection and safety glasses (both are required in the recycling area), and cut-resistant gloves. • Housekeeping and maintenance procedures - For example, there are scheduled procedures for periodically cleaning all room surfaces using a HEPA vacuum, and for maintaining the baghouse. • Medical program - The workers with the highest potential for exposure to toxic substances (e.g., those who service the recycling equipment) receive annual blood lead level testing, audiometry, spirometry, and a physical examination. 3