Wa Doe Wsp Walla Walla Contamination Study 2009 Partd
Download original document:
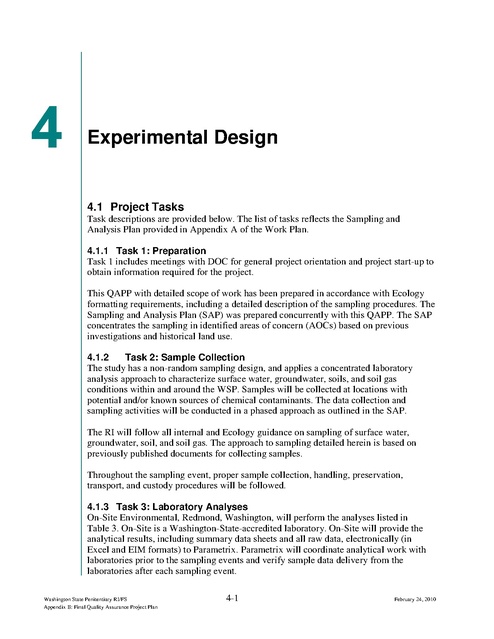
Document text
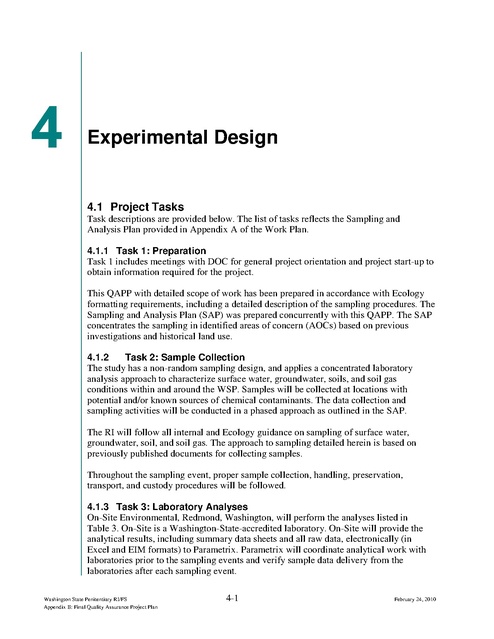
Document text
This text is machine-read, and may contain errors. Check the original document to verify accuracy.
4 Experimental Design 4.1 Project Tasks Task descriptions are provided below. The list of tasks reflects the Sampling and Analysis Plan provided in Appendix A of the Work Plan. 4.1.1 Task 1: Preparation Task 1 includes meetings with DOC for general project orientation and project start-up to obtain information required for the project. This QAPP with detailed scope of work has been prepared in accordance with Ecology formatting requirements, including a detailed description of the sampling procedures. The Sampling and Analysis Plan (SAP) was prepared concurrently with this QAPP. The SAP concentrates the sampling in identified areas of concern (AOCs) based on previous investigations and historical land use. 4.1.2 Task 2: Sample Collection The study has a non-random sampling design, and applies a concentrated laboratory analysis approach to characterize surface water, groundwater, soils, and soil gas conditions within and around the WSP. Samples will be collected at locations with potential and/or known sources of chemical contaminants. The data collection and sampling activities will be conducted in a phased approach as outlined in the SAP. The RI will follow all internal and Ecology guidance on sampling of surface water, groundwater, soil, and soil gas. The approach to sampling detailed herein is based on previously published documents for collecting samples. Throughout the sampling event, proper sample collection, handling, preservation, transport, and custody procedures will be followed. 4.1.3 Task 3: Laboratory Analyses On-Site Environmental, Redmond, Washington, will perform the analyses listed in Table 3. On-Site is a Washington-State-accredited laboratory. On-Site will provide the analytical results, including summary data sheets and all raw data, electronically (in Excel and EIM formats) to Parametrix. Parametrix will coordinate analytical work with laboratories prior to the sampling events and verify sample data delivery from the laboratories after each sampling event. Washington State Penitentiary RI/FS Appendix B: Final Quality Assurance Project Plan 4-1 February 24, 2010 4. Experimental Design 4.1.4 Task 4: Reporting Data validation and database activities: Analytical data will be reviewed and validated to verify they meet project data quality objectives and to identify any limitations of the data, following the process outlined in Ecology QA1 review guidelines (PTI 1989), or other guidelines if specified. These data will be reviewed by comparing calibration, accuracy, and precision results to the QC criteria listed in the method, the laboratory SOP, and the QAPP. If no QA guidelines exist for specific analytes, applicable U.S. Environmental Protection Agency (EPA) National and Regional Data Review guidelines will be used. The contractor will enter data into Ecology’s Environmental Information Management (EIM) database. February 24, 2010 ecol~' eCO)02Y and lIml envi.l"onmenf, environment, inc. 4-2 Washington State Penitentiary RI/FS Appendix B: Final Quality Assurance Project Plan 5 Health and Safety The field work identified in this plan requires careful consideration of health and safety, including: Physical hazards associated with working in the WSP Landfill and within the WSP facility, Site security procedures for the WSP facility, Tool Policy for the WSP facility, Chemical hazards related to sample collection and handling, and Safe driving. The Health and Safety Plan is included in Appendix C of the Work Plan. Decontamination Procedures To the greatest extent possible, disposable and/or dedicated personal protective and sampling equipment will be used to avoid cross-contamination. Pre-cleaned sample bottles will be provided by the laboratory. As much as possible, dedicated sampling equipment will be used. If the equipment is to be reused, it will be scrubbed and washed with non-phosphate detergent and distilled water, followed by a rinse with an appropriate solvent. A final rinse with distilled water also will be performed. If a noticeable oily sheen or petroleum odor is observed after decontamination, sampling bowls and utensils used to process those samples will not be used for subsequent sample processing. Washington State Penitentiary RI/FS Appendix B: Final Quality Assurance Project Plan 5-1 February 24, 2010 This page intentionally left blank. 6 Measurement Procedures The laboratory will analyze the surface water, groundwater, soil, and soil gas samples for the applicable contaminant of concern based on the sample location. For example, potential solvent AOC samples at metal plant #1 will be analyzed for VOCs and metals, and UST area samples will be analyzed for VOCs, SVOCs, and metals. The VOCs will be analyzed using United States Environmental Protection Agency (USEPA) SW-846 Method 8260. With this method, samples are analyzed by gas chromatograph/mass spectrometer (GC/MS). Samples are purged with an inert gas and the analytes are absorbed on a trap. The trap is quickly heated to a high temperature and the analytes are desorbed into a GC equipped with a capillary column. The GC uses a temperature program to separate analytes that are then detected with an MS. Mass spectra of the sample compound and a current laboratory-generated standard must match for positive analyte identification. Analytes are quantified by comparing the response of a major ion relative to an internal standard using a calibration curve developed for each GC/MS. The SVOCs, including PAHs, will be analyzed using USEPA SW-846 Method 8270. Samples will be analyzed by GC/MS following extraction and, if necessary, appropriate sample cleanup and derivatization procedures. With this technique, sample extracts are injected into a GC equipped with a capillary column. The GC uses a temperature program to separate analytes that are then detected with an MS. Mass spectra of the sample compound and a current laboratory-generated standard must match for positive analyte identification. Analytes are quantified by comparing the response of a major ion relative to an internal standard using a calibration curve developed for each GC/MS. TPH-D will be analyzed using Northwest total petroleum hydrocarbons (NWTPH) Method NWTPH-Dx. Samples will be analyzed by GC/flame ionization detector (GC/FID) following extraction and, if necessary, appropriate sample cleanup procedures. Sample extracts are injected into a GC equipped with a capillary column, which uses a temperature program to separate TPH Washington State Penitentiary RI/FS Appendix B: Final Quality Assurance Project Plan 6-1 February 24, 2010 6. Measurement Procedures components that are then detected with an FID. TPH-D is identified by comparing the peak patterns of diesel with retention times of known standards. Diesel is quantified by comparing the sample peak response using a calibration curve developed for each target compound. Metals (excluding mercury) will be analyzed using USEPA 6000 series methods. Samples will be analyzed by either Inductively Coupled Plasma (ICP) or ICP-Mass Spectrometer (ICP-MS) following acid extraction. Sample extracts injected into the ICP or ICP-MS are quantified by comparing instrument response to a calibration curve developed for each analyte. Mercury will be analyzed using USEPA Method 7470 or 7471. Samples will be analyzed by cold vapor absorption spectroscopy (CVS) following acid extraction. Sample extracts injected into the CVS are quantified by comparing instrument response to a calibration curve developed for mercury. Results will be reported for total metals. February 24, 2010 ecol~' eCO)02Y and lIml envi.l"onmenf, environment, inc. 6-2 Washington State Penitentiary RI/FS Appendix B: Final Quality Assurance Project Plan 7 Quality Objectives The data quality objectives (DQOs) for this project are presented below. They identify the seven steps taken to develop this QAPP. 1. State the Problem – Previous investigations have confirmed the presence of VOCs in the groundwater upgradient of the Sudbury Road Landfill and in additional monitoring wells around the WSP landfill. All monitoring wells are considered to be downgradient of the WSP. In several monitoring wells, the concentrations of PCE and TCE have exceeded the MTCA Method A cleanup levels for groundwater. In addition, the following are contaminants of concern based on historical site use: SVOCs, including PAHs PCBs TPHs Metals 2. Identify the Principle Study Questions – The decision will answer these questions: What is the source of the contamination in found in groundwater? Are historical or present activities at the WSP facility responsible for environmental contamination? Is the WSP Landfill responsible for environmental contamination? Alternative actions include eliminating areas from further study or plan and conduct further investigation activities. 3. Identify the Inputs to the Decision – Surface water, groundwater, soils, and soil gas samples will be collected from the identified AOCs. In addition, sample locations may be chosen based on field observations or decisions. Samples will be analyzed for VOCs, SVOCs, PCBs, NWTPH as diesel, and/or total metals, depending on the confirmed or suspected COCs in each AOC. 4. Define the Boundaries of the Study – The primary AOCs are listed in Table 3 and include the WSP Landfill, the former laundry and dry cleaning services area, the former motor pool, UST areas, the former autobody shop and furniture refurbishing area, the hazardous waste accumulation area, boiler ash from the former steam plant, the sign shop, and metal plant #1. Some sampling is dependent on field confirmation of appropriate sampling locations. Washington State Penitentiary RI/FS Appendix B: Final Quality Assurance Project Plan 7-1 February 24, 2010 7. Quality Objectives 5. Develop a Decision Rule – If VOCs and other contaminants of concern are above cleanup limits, then Ecology will consider remedial options. 6. Specify Tolerable Limits on Decision Errors – Sampling should be conducted following guidance appropriate for surface water, groundwater, soil, and soil gas sampling and analyses, e.g., USEPA Test Methods for Evaluating Solid Waste, Physical Chemical Methods, 3rd edition SW-846 (EPA 1986). Analyses should be conducted using standard methods, by Ecology-approved analytical laboratories (alternate laboratories may be used with Ecology approval). Analytical data should meet standard quality control criteria (EPA 1999, EPA 2004). 7. Optimize the Design for Obtaining Data – The Work Plan, QAPP, and SAP present the design for conducting an RI to characterize the nature and vertical and horizontal extent of soil and groundwater contamination across the site and defining the characteristics of soils and groundwater to support a future FS. Acceptance and performance criteria are often specified in terms of precision, accuracy, representativeness, completeness, and comparability (PARCC) parameters. Numerical acceptance criteria cannot be assigned to all PARCC parameters, but general performance goals are established for most data collection activities. PARCC parameters are briefly defined below. Precision Precision measures the reproducibility of measurements under a given set of conditions. Specifically, it is a quantitative measure of the variability of a group of measurements compared with their average value, usually stated in terms of standard deviation or coefficient of variation. It also may be measured as the relative percent difference (RPD) between two values. Precision includes the interrelated concepts of instrument or method detection limits (MDLs) and multiple field sample variance. Sources of this variance are sample heterogeneity, sampling error, and analytical error. Accuracy Accuracy measures the bias of the measurement system. Sources of this error include sampling process, field contamination, preservation, handling, sample matrix, sample preparation, and analysis. Data interpretation and reporting may also be significant sources of error. Typically, analytical accuracy is assessed through the analysis of spiked samples and may be stated in terms of percent recovery or the average (arithmetic mean) of the percent recovery. Blank samples are also analyzed to assess sampling and analytical bias (e.g., sample contamination). February 24, 2010 ecol~' eCO)02Y and lIml envi.l"onmenf, environment, inc. 7-2 Washington State Penitentiary RI/FS Appendix B: Final Quality Assurance Project Plan 7. Quality Objectives Representativeness Representativeness expresses the degree to which data represent a characteristic of a population, a parameter variation at a sampling point, or an environmental condition over time. Representativeness is a qualitative parameter, which is most concerned with proper design of the measurement program. Sample/measurement locations may be biased (judgmental) or unbiased (random or systematic). For unbiased schemes, the sampling must be designed not only to collect samples that represent conditions at a sample location, but also to select sample locations that represent the total area to be sampled. Representativeness also embodies the concept of temporal (for example, seasonal) variations in parameters or conditions. Completeness Completeness for sample collection is defined as the percentage of specified samples listed in the QAPP that were actually collected. The completeness goal will be 90% for this project. Completeness for acceptable data is defined as the percentage of acceptable data out of the total amount of data generated. Acceptable data includes data that passes all QC criteria or data that may not pass all QC criteria but for which appropriate corrective actions are taken. Comparability Comparability is a qualitative parameter expressing the confidence with which one data set may be compared to another. Sample data should be comparable with other measurement data for similar samples and sample conditions. This goal is achieved through the use of standard techniques to collect and analyze samples. Analytical quality objectives for each method are summarized in Table 4. Reporting limits are the practical quantitation limits attainable with these methods. Ranges are presented for some analyte groups due to the large number of compounds analyzed. Analyte-specific reporting limits are presented in Appendix A. Washington State Penitentiary RI/FS Appendix B: Final Quality Assurance Project Plan ecol~' eCO)02Y and lIml envi.l"onmenf, environment, inc. 7-3 February 24, 2010 7. Quality Objectives Table 3 Areas of Concern Ar e a of C on ce rn / Pot ent ia l Ar e a of Con ce rn 1. WSP Landfill (AOC) 2. Former dry cleaning services (AOC) 3. Former motor pool (potential AOC) 4. Former UST areas (potential AOC) 5. Former auto body shop and furniture refurbishing facility (potential AOC) 6. Former hazardous waste accumulation area (potential AOC) 7. Steam plant boiler ash (potential AOC) 8. Sign shop (potential AOC) 9. Metal Plant #1 (potential AOC) Conf ir me d Cont am in ant of C o n ce rn * VOCs, metals TPH-D Su sp ec ted Cont am in ant of C on ce rn VOCs, TPH-D, SVOCs, PAHs (boiler ash fill at various WSP locations) VOCs VOCs, TPH-D, SVOCs TPH-D, SVOCs VOCs, TPH-D, SVOCs VOCs, SVOCs, metals, PCBs and TPH PAHs VOCs VOCs *Analytes that have been detected in previous sampling events. SVOCs TPH TPH-D VOCs PAHs February 24, 2010 ecol~' eCO)02Y and lIml envi.l"onmenf, environment, inc. = = = = = Semi-volatile organic compounds Total petroleum hydrocarbons Total petroleum hydrocarbons-diesel Volatile organic compounds Polycyclic aromatic hydrocarbons 7-4 Washington State Penitentiary RI/FS Appendix B: Final Quality Assurance Project Plan Table 4. Chemical Analytical Parameters, Laboratory Methods, and Method Detection Limits PAHs by Method 8270D SIM Naphthalene 2-Methylnaphthalene 1-Methylnaphthalene Acenaphthylene Acenaphthene Fluorene Phenanthrene Anthracene Fluoranthene Pyrene Benzo[a]anthracene Chrysene Benzo[b]fluoranthene Benzo[k]fluoranthene Benzo[a]pyrene Indeno[1,2,3-c,d]pyrene Dibenz[a,h]anthracene Benzo[g,h,i]perylene Soil MDL 0.000372 0.000281 0.000204 0.000179 0.000282 0.000176 0.000186 0.000151 0.000179 0.000125 0.0000872 0.000103 0.000134 0.0000966 0.0000577 0.0000706 0.0000530 0.0000638 Soil PQL 0.0067 0.0067 0.0067 0.0067 0.0067 0.0067 0.0067 0.0067 0.0067 0.0067 0.0067 0.0067 0.0067 0.0067 0.0067 0.0067 0.0067 0.0067 Soil Units ppm ppm ppm ppm ppm ppm ppm ppm ppm ppm ppm ppm ppm ppm ppm ppm ppm ppm Water MDL 0.0137 0.0195 0.00587 0.00438 0.00617 0.00589 0.00590 0.00494 0.00431 0.00693 0.00418 0.00503 0.00611 0.00553 0.00607 0.00391 0.00353 0.00412 Water PQL 0.10 0.10 0.10 0.10 0.10 0.10 0.10 0.10 0.10 0.10 0.010 0.010 0.010 0.010 0.010 0.010 0.010 0.010 Water Units ppb ppb ppb ppb ppb ppb ppb ppb ppb ppb ppb ppb ppb ppb ppb ppb ppb ppb Semivolatiles by Method 8270D N-Nitrosodimethylamine Pyridine Phenol Aniline bis(2-chloroethyl)ether 2-Chlorophenol n-Decane 1,3-Dichlorobenzene 1,4-Dichlorobenzene Benzyl alcohol 1,2-Dichlorobenzene 2-Methylphenol (o-Cresol) bis(2-Chloroisopropyl)ether (3+4)-Methylphenol (m,p-Cresol) N-Nitroso-di-n-propylamine Hexachloroethane Nitrobenzene Isophorone 2-Nitrophenol 2,4-Dimethylphenol bis(2-Chloroethoxy)methane Soil MDL 0.0103 0.245 0.0128 0.146 0.0135 0.0138 0.0141 0.0118 0.0123 0.0127 0.0118 0.0125 0.0127 0.0118 0.0142 0.0142 0.0157 0.0129 0.0151 0.0162 0.0129 Soil PQL 0.033 0.33 0.033 0.17 0.033 0.033 0.033 0.033 0.033 0.033 0.033 0.033 0.033 0.033 0.033 0.033 0.033 0.033 0.033 0.83 0.033 Soil Units ppm ppm ppm ppm ppm ppm ppm ppm ppm ppm ppm ppm ppm ppm ppm ppm ppm ppm ppm ppm ppm Water MDL 0.195 0.144 0.233 0.266 0.441 0.392 0.302 0.328 0.323 0.305 0.322 0.320 0.360 0.287 0.349 0.393 0.369 0.346 0.392 0.360 0.382 Water PQL 1.0 1.0 1.0 1.0 1.0 1.0 1.0 1.0 1.0 1.0 1.0 1.0 1.0 1.0 1.0 1.0 1.0 1.0 1.0 1.0 1.0 Water Units ppb ppb ppb ppb ppb ppb ppb ppb ppb ppb ppb ppb ppb ppb ppb ppb ppb ppb ppb ppb ppb Page 1 of 6 SPE MDL 0.0154 0.0141 0.0142 0.0108 0.0190 0.0123 0.0101 0.00979 0.00729 0.00479 0.00585 0.00626 0.00618 0.00594 0.0143 0.00603 0.00618 0.00646 SPE PQL 0.10 0.10 0.10 0.10 0.10 0.10 0.10 0.10 0.10 0.10 0.010 0.010 0.010 0.010 0.010 0.010 0.010 0.010 SPE Units ppb ppb ppb ppb ppb ppb ppb ppb ppb ppb ppb ppb ppb ppb ppb ppb ppb ppb Table 4. Chemical Analytical Parameters, Laboratory Methods, and Method Detection Limits Semivolatiles by Method 8270D 2,4-Dichlorophenol Benzoic acid 1,2,4-Trichlorobenzene Naphthalene 4-Chloroaniline Hexachlorobutadiene 4-Chloro-3-methylphenol 2-Methylnaphthalene 1-Methylnaphthalene Hexachlorocyclopentadiene 2,4,6-Trichlorophenol 2,3-Dichloroaniline 2,4,5-Trichlorophenol 2-Chloronaphthalene 2-Nitroaniline 1,4-Dinitrobenzene Dimethylphthalate 1,3-Dinitrobenzene 2,6-Dinitrotoluene 1,2-Dinitrobenzene Acenaphthylene 3-Nitroaniline 2,4-Dinitrophenol Acenaphthene 4-Nitrophenol 2,4-Dinitrotoluene Dibenzofuran 2,3,4,6-Tetrachlorophenol 2,3,5,6-Tetrachlorophenol Diethylphthalate 4-Chlorophenyl-phenylether 4-Nitroaniline Fluorene 4,6-Dinitro-2-methylphenol n-Nitrosodiphenylamine 1,2-Diphenylhydrazine 4-Bromophenyl-phenylether Hexachlorobenzene Pentachlorophenol n-Octadecane Phenanthrene Anthracene Carbazole Soil MDL 0.0126 0.0175 0.0130 0.0147 0.00586 0.0131 0.0112 0.0143 0.0140 0.0102 0.0130 0.0117 0.0128 0.0127 0.00964 0.0108 0.0121 0.00868 0.00822 0.0118 0.0119 0.00612 0.00478 0.0102 0.0116 0.00969 0.0109 0.00843 0.00954 0.0131 0.0110 0.0185 0.00948 0.00699 0.0118 0.0156 0.00984 0.0100 0.00902 0.0199 0.0109 0.0101 0.00910 Soil PQL 0.033 0.17 0.033 0.033 0.033 0.033 0.033 0.033 0.033 0.033 0.033 0.033 0.033 0.033 0.033 0.033 0.033 0.17 0.033 0.033 0.033 0.033 0.033 0.033 0.033 0.17 0.033 0.033 0.033 0.17 0.033 0.033 0.033 0.033 0.033 0.033 0.033 0.033 0.33 0.033 0.033 0.033 0.033 Soil Units ppm ppm ppm ppm ppm ppm ppm ppm ppm ppm ppm ppm ppm ppm ppm ppm ppm ppm ppm ppm ppm ppm ppm ppm ppm ppm ppm ppm ppm ppm ppm ppm ppm ppm ppm ppm ppm ppm ppm ppm ppm ppm ppm Water MDL 0.313 0.0356 0.407 0.429 2.68 0.354 0.339 0.387 0.344 0.265 0.346 0.280 0.206 0.309 0.334 0.322 0.287 0.236 0.377 0.292 0.293 0.249 3.95 0.397 0.222 0.345 0.275 0.287 0.235 0.357 0.228 0.345 0.262 0.267 2.12 0.271 0.170 0.240 0.468 0.335 0.283 0.230 0.276 Page 2 of 6 Water PQL 1.0 5.0 1.0 1.0 10 1.0 1.0 1.0 1.0 1.0 1.0 1.0 1.0 1.0 1.0 1.0 1.0 1.0 1.0 1.0 1.0 1.0 10 1.0 1.0 1.0 1.0 1.0 1.0 1.0 1.0 1.0 1.0 5.0 10 1.0 1.0 1.0 5.0 1.0 1.0 1.0 1.0 Water Units ppb ppb ppb ppb ppb ppb ppb ppb ppb ppb ppb ppb ppb ppb ppb ppb ppb ppb ppb ppb ppb ppb ppb ppb ppb ppb ppb ppb ppb ppb ppb ppb ppb ppb ppb ppb ppb ppb ppb ppb ppb ppb ppb Table 4. Chemical Analytical Parameters, Laboratory Methods, and Method Detection Limits Semivolatiles by Method 8270D Di-n-butylphthalate Fluoranthene Benzidine Pyrene Butylbenzylphthalate bis-2-Ethylhexyladipate 3,3'-Dichlorobenzidine Benzo[a]anthracene Chrysene bis(2-Ethylhexyl)phthalate Di-n-octylphthalate Benzo[b]fluoranthene Benzo[k]fluoranthene Benzo[a]pyrene Indeno[1,2,3-c,d]pyrene Dibenz[a,h]anthracene Benzo[g,h,i]perylene Soil MDL 0.0140 0.00986 0.00128 0.0117 0.0222 0.0148 0.115 0.0125 0.0126 0.0191 0.0131 0.0106 0.0151 0.00922 0.0111 0.00938 0.00920 Soil PQL 0.033 0.033 0.33 0.033 0.033 0.033 0.33 0.033 0.033 0.033 0.033 0.033 0.033 0.033 0.033 0.033 0.033 Soil Units ppm ppm ppm ppm ppm ppm ppm ppm ppm ppm ppm ppm ppm ppm ppm ppm ppm Water MDL 0.276 0.250 1.19 0.271 0.359 0.285 2.13 0.309 0.321 0.172 0.235 0.240 0.316 0.228 0.233 0.257 0.274 Water PQL 1.0 1.0 10 1.0 1.0 1.0 10 1.0 1.0 1.0 1.0 1.0 1.0 1.0 1.0 1.0 1.0 Water Units ppb ppb ppb ppb ppb ppb ppb ppb ppb ppb ppb ppb ppb ppb ppb ppb ppb NWTPH-Dx Diesel Lube Oil Soil MDL 8.78 14.6 Soil PQL 25 50 Soil Units ppm ppm Water MDL 0.0791 0.138 Water PQL 0.25 0.40 Water Units ppm ppm Volatiles by Method 8260B Dichlorodifluoromethane Chloromethane Vinyl Chloride Bromomethane Chloroethane Trichlorofluoromethane 1,1-Dichloroethene Acetone Iodomethane Carbon Disulfide Methylene Chloride (trans) 1,2-Dichloroethene Methyl t-Butyl Ether 1,1-Dichloroethane Vinyl Acetate 2,2-Dichloropropane (cis) 1,2-Dichloroethene Soil MDL 0.628 1.69 0.857 0.536 1.69 0.647 0.210 4.57 0.643 0.281 2.74 0.789 0.173 0.219 0.231 0.253 0.179 Soil PQL 1.0 5.0 1.0 1.0 5.0 1.0 1.0 5.0 5.0 1.0 5.0 1.0 1.0 1.0 5.0 1.0 1.0 Soil Units ppb ppb ppb ppb ppb ppb ppb ppb ppb ppb ppb ppb ppb ppb ppb ppb ppb Water MDL 0.143 0.0313 0.0399 0.0978 0.175 0.0599 0.0459 0.562 0.343 0.0258 0.175 0.0335 0.0507 0.0426 0.163 0.0702 0.0380 Water PQL 0.20 1.0 0.20 0.20 1.0 0.20 0.20 5.0 1.0 0.20 1.0 0.20 0.20 0.20 2.0 0.20 0.20 Water Units ppb ppb ppb ppb ppb ppb ppb ppb ppb ppb ppb ppb ppb ppb ppb ppb ppb Page 3 of 6 Table 4. Chemical Analytical Parameters, Laboratory Methods, and Method Detection Limits Volatiles by Method 8260B 2-Butanone Bromochloromethane Chloroform 1,1,1-Trichloroethane Carbon Tetrachloride 1,1-Dichloropropene Benzene 1,2-Dichloroethane Trichloroethene 1,2-Dichloropropane Dibromomethane Bromodichloromethane 2-Chloroethyl Vinyl Ether (cis) 1,3-Dichloropropene Methyl Isobutyl Ketone Toluene (trans) 1,3-Dichloropropene 1,1,2-Trichloroethane Tetrachloroethene 1,3-Dichloropropane 2-Hexanone Dibromochloromethane 1,2-Dibromoethane Chlorobenzene 1,1,1,2-Tetrachloroethane Ethylbenzene m,p-Xylene o-Xylene Styrene Bromoform Isopropylbenzene Bromobenzene 1,1,2,2-Tetrachloroethane 1,2,3-Trichloropropane n-Propylbenzene 2-Chlorotoluene 4-Chlorotoluene 1,3,5-Trimethylbenzene tert-Butylbenzene 1,2,4-Trimethylbenzene sec-Butylbenzene 1,3-Dichlorobenzene p-Isopropyltoluene Soil MDL 1.23 0.489 0.315 0.286 0.366 0.346 0.142 0.266 0.554 0.302 0.351 0.273 3.29 0.197 0.518 0.291 0.203 0.375 0.297 0.229 0.679 0.298 0.199 0.196 0.254 0.168 0.401 0.273 0.178 0.538 0.162 0.244 0.462 0.306 0.179 0.325 0.336 0.258 0.262 0.209 0.183 0.278 0.242 Soil PQL 5.0 1.0 1.0 1.0 1.0 1.0 1.0 1.0 1.0 1.0 1.0 1.0 5.0 1.0 5.0 5.0 1.0 1.0 1.0 1.0 5.0 1.0 1.0 1.0 1.0 1.0 2.0 1.0 1.0 1.0 1.0 1.0 1.0 1.0 1.0 1.0 1.0 1.0 1.0 1.0 1.0 1.0 1.0 Soil Units ppb ppb ppb ppb ppb ppb ppb ppb ppb ppb ppb ppb ppb ppb ppb ppb ppb ppb ppb ppb ppb ppb ppb ppb ppb ppb ppb ppb ppb ppb ppb ppb ppb ppb ppb ppb ppb ppb ppb ppb ppb ppb ppb Water MDL 0.523 0.0710 0.0527 0.0336 0.0329 0.0612 0.0241 0.0359 0.0484 0.0542 0.0661 0.0217 0.210 0.0613 0.141 0.0291 0.0506 0.0978 0.0457 0.0660 0.0969 0.0382 0.0952 0.0340 0.0465 0.0243 0.0333 0.0255 0.0231 0.0928 0.0284 0.117 0.0557 0.0939 0.0188 0.0401 0.0402 0.0258 0.0243 0.0217 0.0220 0.0266 0.0257 Page 4 of 6 Water PQL 5.0 0.20 0.20 0.20 0.20 0.20 0.20 0.20 0.20 0.20 0.20 0.20 1.0 0.20 2.0 1.0 0.20 0.20 0.20 0.20 2.0 0.20 0.20 0.20 0.20 0.20 0.40 0.20 0.20 1.0 0.20 0.20 0.20 0.20 0.20 0.20 0.20 0.20 0.20 0.20 0.20 0.20 0.20 Water Units ppb ppb ppb ppb ppb ppb ppb ppb ppb ppb ppb ppb ppb ppb ppb ppb ppb ppb ppb ppb ppb ppb ppb ppb ppb ppb ppb ppb ppb ppb ppb ppb ppb ppb ppb ppb ppb ppb ppb ppb ppb ppb ppb Table 4. Chemical Analytical Parameters, Laboratory Methods, and Method Detection Limits Volatiles by Method 8260B 1,4-Dichlorobenzene 1,2-Dichlorobenzene n-Butylbenzene 1,2-Dibromo-3-chloropropane 1,2,4-Trichlorobenzene Hexachlorobutadiene Naphthalene 1,2,3-Trichlorobenzene Volatiles by Method 8260B/SIM Vinyl Chloride ICP Metals by Method 200.7/6010B Antimony Arsenic Beryllium Cadmium Chromium Copper Lead Nickel Selenium Silver Thallium Zinc Soil MDL 0.269 0.321 0.222 0.940 0.383 0.503 0.314 0.259 Soil PQL 1.0 1.0 1.0 5.0 1.0 5.0 1.0 1.0 Soil Units ppb ppb ppb ppb ppb ppb ppb ppb Water MDL 0.123 0.107 0.0394 0.468 0.0398 0.0529 0.0547 0.0586 Water PQL 0.20 0.20 0.20 1.0 0.20 0.20 1.0 0.20 Water Units ppb ppb ppb ppb ppb ppb ppb ppb Soil MDL Soil PQL Soil Units Water MDL Water PQL 0.020 Water Units ppb Soil MDL 3.55 1.65 0.0103 0.0744 0.155 0.384 1.18 0.389 3.37 0.201 9.64 0.361 Soil PQL 5.0 10 0.50 0.50 0.50 0.50 5.0 2.5 10 0.50 10 2.5 Soil Units ppm ppm ppm ppm ppm ppm ppm ppm ppm ppm ppm ppm Water MDL 53.1 25.8 0.223 1.49 4.40 5.98 35.6 7.34 52.5 5.54 135 4.95 Water PQL 100 200 10 10 10 10 100 50 200 10 200 50 Water Units ppb ppb ppb ppb ppb ppb ppb ppb ppb ppb ppb ppb Page 5 of 6 Dissolved MDL 63.2 44.1 0.466 1.17 3.26 6.42 20.9 7.99 102 5.41 184 5.85 Dissolved PQL 100 200 10 10 10 10 100 50 200 10 200 50 Dissolved Units ppb ppb ppb ppb ppb ppb ppb ppb ppb ppb ppb ppb Table 4. Chemical Analytical Parameters, Laboratory Methods, and Method Detection Limits ICP/MS Metals by Method 200.8/6020 Antimony Arsenic Beryllium Cadmium Chromium Copper Lead Nickel Selenium Silver Thallium Zinc Soil MDL 0.0180 0.0104 0.00720 0.00461 0.0438 0.0153 0.0353 0.0178 0.0485 0.0163 0.00547 0.133 Soil PQL 5.0 10 0.50 0.50 0.50 0.50 5.0 2.5 10 0.50 5.0 2.5 Soil Units ppm ppm ppm ppm ppm ppm ppm ppm ppm ppm ppm ppm Water MDL 0.160 0.577 0.230 0.0401 0.654 0.321 0.218 0.303 1.06 0.199 0.0284 2.32 Water PQL 5.5 3.3 11 4.4 11 11 1.1 56 5.6 11 5.6 56 Water Units ppb ppb ppb ppb ppb ppb ppb ppb ppb ppb ppb ppb Mercury by Method 7470A/7471A Mercury Mercury (low) Soil MDL 0.000247 n/a Soil PQL 0.25 n/a Soil Units ppm n/a Water MDL 0.0126 0.0145 Water PQL 0.50 0.038 Water Units ppb ppb Page 6 of 6 Dissolved MDL 0.0441 0.0661 0.0517 0.0154 0.109 0.304 0.0123 0.0364 0.127 0.0609 0.0133 0.487 Dissolved PQL 5.0 1.0 10 4.0 10 10 1.0 40 5.0 10 5.0 50 Dissolved Units ppb ppb ppb ppb ppb ppb ppb ppb ppb ppb ppb ppb 8 Quality Control Procedures 8.1 Field Table 5 specifies the sample volumes, types of containers, preservation, and holding times for all analyses. Field Logbooks and Data Forms Field logbooks and data forms/sheets will be used to document daily activities and observations. Documentation will be sufficient to enable participants to accurately and objectively reconstruct events that occurred during the project at a later time. Entries will be made in waterproof ink, dated, and signed. Project-specific field data forms/sheets will be used to capture field operations and observations. If corrections to the field logbooks are necessary, they will be made by drawing a single line through the original entry (so that the original entry is legible) and writing the corrected entry alongside. The correction will be initialed and dated. Corrected errors may require a footnote explaining the correction. Custody Procedures The primary objective of chain of custody procedures is to provide an accurate written or computerized record that can be used to trace the possession and handling of a sample from collection to completion of all required analyses. A sample is in custody when it is: In someone’s physical possession In someone’s view Locked up Kept in a secured area that is restricted to authorized personnel Washington State Penitentiary RI/FS Appendix B: Final Quality Assurance Project Plan 8-1 February 24, 2010 8. Quality Control Procedures Table 5 Parameter VOCs Laboratory TBD Method 8260 Matrix Soil Container 3 Encore® Samplers Preservation Cool to ≤ 6oC VOCs TBD 8260 Water 3 VOA vials VOCs Field TBD Soil Gas Soil TBD SVOCs Modified 8260 8270 HCl pH < 2; Cool to ≤ 6oC Cool to ≤ 6oC SVOCs TBD 8270 Water PAHs TBD 8270 Soil PAHs TBD 8270 Water TPH-D TBD NWTPH-Dx Soil TPH-D TBD NWTPH-Dx Water Metals TBD Soil Metals TBD 6000/7000 series 6000/7000 series Key: HCl Hg HNO3 SVOCs TBD TPHs VOCs = = = = = = = February 24, 2010 ecol~' eCO)02Y Sample Volumes, Containers, Preservation, and Holding Times for Target Analytes and lIml envi.l"onmenf, environment, inc. Water 8-oz glass jar, Teflon lid 1-liter amber glass, Teflon lid 8-oz glass jar, Teflon lid 1-liter amber glass, Teflon lid 8-oz glass jar, Teflon lid 1-liter amber glass, Teflon lid 500-ml Teflon bottle Cool to ≤ 6oC 8-oz glass jar, Teflon lid HNO3 pH < 2; Cool to ≤ 6oC Cool to ≤ 6oC Cool to ≤ 6oC Cool to ≤ 6oC HCl pH < 2; Cool to ≤ 6oC Cool to ≤ 6oC Cool to ≤ 6oC Holding Time 7 days for extraction, then 14 days until analysis 14 days to analysis 14 days to analysis 14 days for extraction, then 40 days until analysis 7 days for extraction, then 40 days until analysis 14 days for extraction, then 40 days until analysis 7 days for extraction, then 40 days until analysis 14 days for extraction, then 40 days until analysis 14 days for extraction, then 40 days until analysis 6 months to analysis, except Hg (28 days) 6 months to analysis, except Hg (28 days) Hydrochloric acid Mercury Nitric acid Semivolatile organic compounds To be determined Total petroleum hydrocarbons Volatile organic compounds 8-2 Washington State Penitentiary RI/FS Appendix B: Final Quality Assurance Project Plan 8. Quality Control Procedures Field Custody Procedures The following guidance will be used to ensure proper control of samples while in the field: As few people as possible will handle the samples. The sample collector will be responsible for the care and custody of collected samples until they are transferred to another person or dispatched properly under chain of custody rules. The sample collector will record sample data in the field logbook and/or on field data forms/sheets. The sampling team leader will determine whether proper custody procedures were followed during the fieldwork and will decide whether additional samples are required. When transferring custody (i.e., releasing samples to a shipping agent), the following will apply: The container in which the samples are packed will be sealed and accompanied by two copies of the chain of custody records. When transferring samples, the individuals relinquishing and receiving them must sign, date, and note the time on the chain of custody record. This record will document sample custody transfer. Samples will be dispatched to the laboratory for analysis with separate chain of custody records accompanying each shipment. Shipping containers will be sealed with custody seals for shipment to the laboratory. The chain of custody records will be signed by the relinquishing individual, and the method of shipment, name of courier, and other pertinent information will be entered on the chain of custody record before placement in the shipping container. All shipments will be accompanied by chain of custody records identifying their contents. The original record will accompany the shipment. The other copies will be distributed appropriately to the site team leader and site manager. If samples are sent by common carrier, a bill of lading will be used. Freight bills and bills of lading will be retained as part of the permanent documentation. Laboratory Custody Procedures A designated sample custodian at the laboratory will accept custody of the shipped samples from the carrier and enter preliminary information about the package into a package or sample receipt log, including the initials of the person delivering the package and the status of the custody seals on the coolers (i.e., broken versus unbroken). The custodian responsible for sample log-in will follow the laboratory’s SOP for opening the package, checking the contents, and verifying Washington State Penitentiary RI/FS Appendix B: Final Quality Assurance Project Plan ecol~' eCO)02Y and lIml envi.l"onmenf, environment, inc. 8-3 February 24, 2010 8. Quality Control Procedures that the information on the chain of custody agrees with the samples received. The laboratory will follow its internal chain of custody procedures as stated in the laboratory QA manual. Field QC Samples Field QC samples for this project will include: field (equipment rinsate) blank and field duplicate for collection of sufficient sample volume to allow the laboratories to conduct the QC analyses identified in Table 6. The field/rinsate blank is used to evaluate potential contamination from sampling equipment. The matrix spike (MS) and matrix spike duplicate (MSD) taken from the duplicate sample are co-located samples collected concurrently with one sample; the laboratory uses the MSs/MSDs to measure analytical precision and accuracy. Table 6 Field Quality Control Samples for Each Parameter monitored at POTWs Equipment/ a b Method Parameter Matrix Rinsate Blank Field Duplicate MS/MSD 8260 VOCs Soil 1 per 20 samples 1 per 20 samples 1 per 20 samples 8260 VOCs Water 1 per 20 samples 1 per 20 samples 1 per 20 samples 8260 VOCs Soil Gas NA NA NA 8270 SVOCs Soil 1 per 20 samples 1 per 20 samples 1 per 20 samples 8270 SVOCs Water 1 per 20 samples 1 per 20 samples 1 per 20 samples 8270 PAHs Soil 1 per 20 samples 1 per 20 samples 1 per 20 samples 8270 PAHs Water 1 per 20 samples 1 per 20 samples 1 per 20 samples 8082 PCBs Water 1 per 20 samples 1 per 20 samples 1 per 20 samples NWTPH-Dx TPH-D Soil 1 per 20 samples 1 per 20 samples 1 per 20 samples NWTPH-Dx TPH-D Water 1 per 20 samples 1 per 20 samples 1 per 20 samples 6000/7000 series Metals Soil 1 per 20 samples 1 per 20 samples 1 per 20 samples 6000/7000 series Metals Water 1 per 20 samples 1 per 20 samples 1 per 20 samples a – A minimum of one rinsate blank will be collected per 20 samples of the same matrix collected using nondedicated sampling equipment. b – A minimum of one MS/MSD for organic analyses (MS/Duplicate for metals) will be analyzed per 20 samples of the same matrix. Key: MS/MSD = Matrix spike/matrix spike duplicate. NA = Not applicable. PAHs = Polycyclic aromatic hydrocarbons. BNAs = Base/neutral/acid extractable compounds (semivolatiles). NA = Not applicable. NWTPH-Dx = Northwest total petroleum hydrocarbon – diesel. TBD = To be determined. SVOCs = Semivolatile organic compounds. VOCs = Volatile organic compounds. The time that each individual grab sample was collected will also be noted before the samples are composited on the site. One equipment rinsate blank for every twenty samples will be collected. The blanks will be collected by filling sample bottles using the same equipment used for actual sample collection. February 24, 2010 ecol~' eCO)02Y and lIml envi.l"onmenf, environment, inc. 8-4 Washington State Penitentiary RI/FS Appendix B: Final Quality Assurance Project Plan 8. Quality Control Procedures One field duplicate will be collected for every twenty samples for each analysis. Clean blank water field (equipment rinsate) blanks will be provided by the laboratory. A modified one-person clean hands/dirty hands sampling technique will be used to collect the samples. 8.2 Laboratory Laboratory QC samples are summarized in Table 7. Detailed QA procedures are documented in each subcontracted laboratory’s quality assurance manual. One QC target for this project is for each lab to extract and analyze all the samples collected during each event in a single batch. By doing this, a single set of quality control parameters will be applicable to all samples collected during each sampling event. Table 7 Analytical Laboratory Quality Control Samples Method Method Parameter Blank LCS 8260 VOCs 1/batch/matrix 1/batch/matrix 8270 SVOCs 1/batch/matrix 1/batch/matrix NWTPH TPH-D 1/batch/matrix 1/batch/matrix 6000/7000 Metals 1/batch/matrix 1/batch/matrix series Key: LCS – Laboratory control sample. MS – Matrix spike. MSD – Matrix spike duplicate. NA – Not applicable. PAHs – Polycyclic aromatic hydrocarbons. BNAs – Base/neutral/acid extractable compounds (semivolatiles). NWTPH-Dx – Northwest total petroleum hydrocarbons – diesel. TBD – To be determined. SVOCs – Semivolatile organic compounds. VOCs – Volatile organic compounds. *One duplicate per batch per matrix is required for metals. MS 1/batch/matrix 1/batch/matrix 1/batch/matrix 1/batch/matrix MSD 1/batch/matrix 1/batch/matrix 1/batch/matrix * The method blank is used to assess potential contamination from sample handling in the laboratory. The laboratory control sample (LCS) is sometimes referred to as a blank spike. The LCS is used to measure the accuracy of the laboratory by determining the ability of the lab to recover known amounts of target analytes in the absence of matrix effects. Known amounts of target analytes are added to the MS and MSD in the laboratory. The laboratories measure the percent recovery of these compounds to estimate accuracy. Analytical precision is estimated by comparing the MS and MSD recoveries. The matrix spikes allow the laboratory to assess matrix interferences. Precision is also impacted by field variability since separate samples are being collected. Washington State Penitentiary RI/FS Appendix B: Final Quality Assurance Project Plan ecol~' eCO)02Y and lIml envi.l"onmenf, environment, inc. 8-5 February 24, 2010 This page intentionally left blank. 9 Data Verification, Review, and Validation 9.1 Data Verification Field data and observations will be recorded in detailed log books. All subcontracted laboratories will provide both electronic and hard copy data packages for data. Each data package will include a case narrative discussing any problems with the analyses, alterations, if any, made to the methods, and an explanation of data qualifiers. The data package will include all relevant QC results. QC information will be used to evaluate the accuracy and precision of the data and to determine whether measurement data quality objectives were met. A Quality Assurance level 1 (QA1) analytical data review will be conducted following the process outlined in Ecology QA1 review guidelines (PTI 1989). QA1 includes review of case narratives and laboratory data. Reviews verify that methods specified in this QAPP were followed, calibrations and QC checks are provided for all samples, and data are correct and complete. Evaluation criteria include holding times, calibrations, blanks, detection limits, control samples, spike recoveries and relative percent differences, and laboratory-applied data qualifiers. Significant laboratory findings will be discussed with the applicable laboratory project managers. QA summary memoranda will be prepared for the record. Impacts, if any, to the data will be summarized and addressed in the final report. Field data will also be evaluated for QA. Impacts, if any, to the data will be summarized and addressed in the final report. All reviews will be completed by the QA lead and an experienced data validation chemist, and checked by the project manager. Washington State Penitentiary RI/FS Appendix B: Final Quality Assurance Project Plan 9-1 February 24, 2010 9. Data Verification, Review, and Validation 9.2 Data Quality (Usability) Assessment Once the data verification process has been completed, the project manager will determine whether the data are adequate for the calculations, determinations, and decisions for which this project was conducted. If the results are acceptable, data analysis will be completed. Data analysis will include, but not be limited to, compiling summary statistics and constructing plots to examine the distribution of contaminant concentrations in samples spatially, temporally, and by source (e.g., industrial versus nonindustrial). 9.3 Data Validation Analytical data will be validated to verify they meet project data quality objectives and to identify any limitations of the data, following the process outlined in Ecology QA1 review guidelines (PTI 1989). These data will be validated by comparing calibration, accuracy, and precision results to the QC criteria listed in the method, the laboratory SOP, and the QAPP. If no QA guidelines exist for specific analytes, then applicable USEPA National and Regional Data Review guidelines will be used. 9.4 Data Management Procedures Field and laboratory project data will be entered into Excel spreadsheets. Entries will be independently verified for accuracy. All applicable data will be entered into Ecology’s Environmental Information Management system (EIM). Entries will be independently verified for accuracy. 9.5 Audits and Reports The subcontracted laboratory will conduct performance and system audits of their procedures. Ecology’s Accreditation Program determines whether external laboratories may be used to analyze samples. The contractor will prepare the following reports for this project: Draft Summary Technical Report Final Summary Technical Report Project data will be entered into: January7, 2010 ecol~' eCO)02Y and lIml envi.l"onmenf, environment, inc. Ecology’s EIM Ecology’s Phase 2 Access database 9-2 Washington State Penitentiary RI/FS Appendix B: Final Quality Assurance Project Plan 10 References Ecology, July 2004a. Washington State Department of Ecology, Guidelines for Preparing Quality Assurance Project Plans for Environmental Studies, Publication Number 04-03-030. EPA. 1986. USEPA Test Methods for Evaluating Solid Waste, Physical Chemical Methods, 3rd edition SW-846 ______. 1999. EPA, USEPA Contract Laboratory Program National Functional Guidelines for Organic Data Review, EPA-540/R-99-008 (PB99-963506), October 1999. ______. 2004. Review, OSWER 9240.1-45, EPA 540-R-04-004, October 2004. PTI. 1989. Data Validation Guidance Manual for Selected Sediment Variables. Prepared by PTI Environmental Services for Washington Department of Ecology, Olympia, Washington. Washington State Penitentiary RI/FS Appendix B: Final Quality Assurance Project Plan 10-1 February 24, 2010 This page intentionally left blank. A Meeting Notes This is Appendix A to the document: Appendix B: Final Quality Assurance Project Plan Washington State Penitentiary RI/FS Appendix B: Final Quality Assurance Project Plan A-1 February 24, 2010 This page intentionally left blank. C Health and Safety Plan Washington State Penitentiary RI/FS Appendix C: Health and Safety Plan February 24, 2010 This page intentionally left blank Project Health and Safety Plan Washington State Penitentiary Remedial Investigation/ Feasibility Study Washlng(on Washington Siale State DEPARTMENT D6WlTMEHT Of CDRRECTlONS CORRECTIONS February 2010 Project Health and Safety Plan Washington State Penitentiary Remedial Investigation/Feasibility Study Prepared for Washington State Department of Corrections Departments of General Administration/Corrections (DGA/DOC) Team Program Box 41112 Olympia, WA 98504 Prepared by Parametrix 1231 Fryar Avenue Sumner, WA 98390-1516 T. 253.863.5128 F. 253.863.0946 www.parametrix.com February 2010 │ 215-2662-004 (01/03) CITATION Parametrix. 2010. Project Health and Safety Plan Washington State Penitentiary Remedial Investigation/Feasibility Study. Prepared by Parametrix, Sumner, Washington. February 2010. Project Health and Safety Plan Washington State Penitentiary Remedial Investigation/Feasibility Study Washington State Department of Corrections TABLE OF CONTENTS PROJECT HEALTH AND SAFETY INFORMATION SHEET .................................... v 1. INTRODUCTION ................................................................................................. 1 2. SCOPE OF WORK .............................................................................................. 1 3. HAZARD ANALYSIS ........................................................................................... 1 3.1 PHYSICAL HAZARD ANALYSIS ......................................................................... 1 3.2 CHEMICAL HAZARD ANALYSIS ........................................................................ 5 4. MONITORING OF CHEMICAL HAZARDS .......................................................... 5 5. PERSONAL PROTECTIVE EQUIPMENT ........................................................... 6 6. SITE CONTROL AND DECONTAMINATION ...................................................... 7 7. TRAINING ........................................................................................................... 8 8. PROJECT/EMERGENCY CONTACTS AND PROCEDURES ............................. 8 8.1 EMERGENCY ASSISTANCE ................................................................................. 9 8.2 POTENTIAL INCIDENTS ....................................................................................... 9 8.3 ADVERSE WEATHER CONDITIONS ................................................................. 10 9. STANDARD OPERATING PROCEDURES ....................................................... 10 10. REFERENCES .................................................................................................. 11 LIST OF FIGURES 1 WSP RI Project Vicinity Map ................................................................................... 3 LIST OF TABLES 1 Physical Hazard Analysis for Project Activities, WSP RI/FS ................................... 2 2 Air Monitoring and Action Levels ............................................................................ 5 3 Exposure Concentrations for Potential Chemicals of Concern ................................. 6 4 Project and Emergency Contacts ............................................................................... 8 APPENDICES A Forms B Map and Directions to Hospital C Standard Operating Procedures February 2010 │ 215-2662-004 (01/03) i Project Health and Safety Plan Washington State Penitentiary Remedial Investigation/Feasibility Study Washington State Department of Corrections KEY TERMS COCs chemicals of concern CPR cardiopulmonary resuscitation DOC Department of Corrections FS feasibility study HASP Health and Safety Plan HAZWOPER Hazardous Waste Operation HVOCs halogenated volatile organic compounds HWA HWA Geosciences Incorporated NIOSH National Institute of Safety and Health PID photoionization detector PPE personal protective equipment RI remedial investigation SOPs standard operating procedures VOCs volatile organic compounds WSP Washington State Penitentiary February 2010 │ 215-2662-004 (01/03) iii Project Health and Safety Plan Washington State Penitentiary Remedial Investigation/Feasibility Study Washington State Department of Corrections PROJECT HEALTH AND SAFETY INFORMATION SHEET Project Manager: Mike Warfel, Parametrix Date: February 25, 2010 Project Name: Washington State Penitentiary RI/FS Project No.: 215-2662-004 Site Name and Address: Washington State Penitentiary 1313 N. 13th Street, Walla Walla, Washington Client Contact: Jack Olson Site Description: Over many years of operation, the Washington State Penitentiary used hazardous chemicals in its dry cleaning, machine repair, metalworking, and refueling activities. The purpose of the Remedial Investigation is to gather more information to determine where and how much contamination is present in soil and groundwater. The Feasibility Study will evaluate cleanup alternatives in preparation for a cleanup action. Estimated Date of Fieldwork: Spring 2010 Phone: Due Date of Health & Safety Plan: (360) 725-8342 February 25, 2010 Type of Work to be Performed (check all that apply): File Review Notes: Surveying Environmental Sampling Engineering and/or Maintenance Work (specify below) Inspection Parametrix will be performing a subsurface soil and groundwater investigation at the three sites involving utility location by conventional and air knife methods, direct push boring and well installation, and sampling of soil and groundwater in preparation for road improvements. Collection of Field Samples: Groundwater Surface Water Biological Notes: Soil Air Entry into confined spaces (e.g., storage tank, sewer, utility vault, trenches, or other excavations) Wastes (specify) Other (please specify) – Soil Gas Identified contaminants of concern include petroleum hydrocarbons, volatile and semivolatile organic compounds (VOCs and SVOCs), and metals in soil and groundwater water. High levels of noise and safety hazards may be present from sampling equipment. Role of Parametrix at site (check one): Prime Contractor Notes: Subcontractor to: Parametrix personnel will be conducting the remedial activities shown below. Drilling will be completed by a subcontractor. Drilling Operations and Maintenance Surveying Remedial Actions Construction Field Team Leader: To Be Determined Health and Safety Officers: Corporate: Sheila McConnell, CIH Site: To Be Determined Field Sampling Regulatory/Enforcement Status of Site (check all that apply): Superfund Site Enforcement Actions (please check all that apply and describe) Federal State – Department of Ecology Agreed Order Local Voluntary Investigations by Site Owner On-site inspectors present? (If yes, provide names, phone numbers, and agency affiliations.) Notes: February 2010 │ 215-2662-004 (01/03) v Project Health and Safety Plan Washington State Penitentiary Remedial Investigation/Feasibility Study Washington State Department of Corrections 1. INTRODUCTION The Department of Corrections (DOC) has retained Parametrix to conduct a remedial investigation (RI) and feasibility study (FS) of the Washington State Penitentiary (WSP) located at Walla Walla, Washington (Figure 1). This Project Health and Safety Plan (HASP) presents project specific health and safety requirements for the RI. This project HASP is designed for use in conjunction with the Parametrix Health and Safety Manual (Parametrix 2003). The health and safety requirements presented in this document are applicable to Parametrix employees and Parametrix subcontractors working on the project or persons visiting the job site during remediation activities. Any modification or additions to this project HASP will be completed as an addendum in the form of a technical memorandum. 2. SCOPE OF WORK Parametrix’s primary role is to conduct a surface and subsurface soil, soil gas, and groundwater investigation where the proposed activities include: • • Observation of utility location services provided by a subcontractor. • • • Collection of surface soil samples using hand tools and test pits. • Collection of samples of soil cuttings from drilling. Observation of drilling services to be provided by a subcontractor, using the sonic drilling method. Collection of soil gas samples. Collection of soil and groundwater samples during drilling. The overall hazard level associated with the above activities is expected to be low on a scale of low, moderate, and high. An analysis of potential hazards associated with the activities is presented in Section 3. 3. HAZARD ANALYSIS A hazard analysis was conducted for the field activities described in Section 2 to identify potential health and safety concerns. The hazard analysis will be updated if additional project-related hazards are identified. 3.1 PHYSICAL HAZARD ANALYSIS Physical hazards that may be encountered at the site are presented below in Table 1. February 2010 │ 215-2662-004 (01/03) 1 Project Health and Safety Plan Washington State Penitentiary Remedial Investigation/Feasibility Study Washington State Department of Corrections Table 1. Physical Hazard Analysis for Project Activities, WSP RI/FS Activity Drilling Hazard Slip/Trips/Falls Flying Debris/Soil and Splashing Liquids Drilling Rig Pinch Points Noise Falling Objects Utility Contact Heat or Cold Stress Environmental Sampling Slip/Trips/Falls Flying Debris/Soil and Splashing Liquids • • • • • • Wear safety glasses or other applicable eye protection. • • • • • • • • • • • • • • • • • • • Wear hardhat and steel-toed footwear. Know the location of drill emergency stop switch. Confirm the stop switch procedure with the driller Maintain eye contact with driller. Don’t move drill rig with mast up. Check minimum distance to power lines. • • • Keep work areas free of debris, etc. Clean up work areas following completion of activities. Watch for debris and other hazards that may be present from past site operations. Follow required safety procedures. • • Identify pinch points prior to starting equipment. Be aware of equipment location and body placement. Know the location of drill emergency stop switch. Maintain eye contact with operator. Wear earplugs while equipment is operating. Wear hardhat and steel-toed footwear. Perform a utility locate prior to drilling. Keep at least three feet from utility markings. Wear several layers of clothing during cold weather Dress in cotton clothing during hot weather. Take frequent breaks to warm up in running vehicles during cold weather. Take frequent breaks to cool down in the shade during hot weather. Watch other workers on site for signs of heat or cold stress during the workday. Wear safety glasses or other applicable eye protection. Working Around Water • • • Use buddy system. Wear shaded safety glasses to reduce glare from water. Do not enter or work over water unless wearing a personal floatation device. Contact with Contaminated Media and Preservatives • • Collect and handle samples wearing appropriate PPE. Employ proper shipping and packing procedures. Cuts/Abrasions • • • • • • • Use proper cutting tools. Be careful with sharp objects. Do not cut towards yourself. Conduct sampling using proper operation of the sampling equipment. Overhead Lifting 2 Mitigation Keep work areas free of debris, etc. Clean up work areas following completion of activities. Watch for debris and other hazards that may be present from past site operations. Follow required safety procedures. Use proper illumination. Wear hardhat and steel toed footwear. Maintain eye contact with driller and other heavy equipment operators. Use proper lifting equipment and techniques when moving equipment, tools, drums, etc. February 2010│ 215-2662-004 (01/03) WASHINGTON Groundwater Flow Source: Google Earth Pro, 2008. Washington State Penitentiary Property Boundary See Figure 2 Walla Walla Washington State Penitentiary Landfill MW-5 MW-2 MW-9 MW-4 Sudbury Landfill MW-3 Burlington Northern Pacific Rail Road MW-7 MW-10 MW-1 MW-8 MW-8A MW-11 MW-6 CITY OF WALLA WALLA Southern Drainage Pond Key: Sudbury Road Landfill Groundwater Monitoring Well Mill Creek Washington State Penitentiary Groundwater Monitoring Well Washington State Penitentiary Property Boundary Washington State Penitentiary Landfill Sudbury Landfill Note: Monitoring well locations are approximate. ecology and environment, inc. & International Specialists in the Environment Seattle, Washington 0 N 1072 Approximate Scale in Feet 2144 WASHINGTON STATE PENITENTIARY Walla, Walla, Washington Figure 1 SITE LOCATION MAP Date: 6/9/09 Drawn by: AES 10:002330WD2703\fig 1 Project Health and Safety Plan Washington State Penitentiary Remedial Investigation/Feasibility Study Washington State Department of Corrections 3.2 CHEMICAL HAZARD ANALYSIS Parametrix will be working with staff from HWA Geosciences Incorporated (HWA). HWA has conducted several investigations within the project area. Petroleum hydrocarbons, halogenated volatile organic compounds (HVOCs), and various metals have been identified as potential chemicals of concern. Precautions will be taken by all persons conducting remedial activities at the site to minimize exposure to potential chemicals of concern. Information on reducing contact with potential chemicals of concern is presented in the following sections. This section will be updated if additional chemicals of concern (COCs) associated with other locations within the WSP RI/FS project are identified. 4. MONITORING OF CHEMICAL HAZARDS Air monitoring with a photoionization detector (PID) will be performed when sampling soil suspected of containing hydrocarbons or HVOCs to determine if the level of Personal Protective Equipment (Section 5) will need to be upgraded from Level D to Level C, which requires respiratory protection. Air monitoring and action levels are listed in Table 2, and exposure limits for potential contaminants of concern are shown in Table 3. If a change in conditions (i.e., odor, etc.) indicates a need to upgrade personal protective equipment (PPE), the Parametrix Site Health and Safety Officer will upgrade the PPE to Level C, and the Corporate Health and Safety Officer and the site Task Manager will be notified immediately. Contact information is presented in Chapter 8. All air-monitoring and instrumentation-calibration data will be recorded in the field notebook. Air monitoring instruments will be calibrated and maintained in accordance with the manufacturer’s specifications. Table 2. Air Monitoring and Action Levels Exposure Screening for organic and inorganic vapors Monitoring Description Method PID A PID will be used to assess potential exposures to organic vapors. Action Level >10 ppm sustained for 5 minutes Action • Terminate operation and move • • • • Metals Notes: Visual Observation Exposure to airborne particulates which could contain metals will be assessed using visual observation methods Visible emissions upwind Ventilate area, as needed Investigate cause Upgrade to Level C Respirator with organic vapor/HEPA cartridge, if warranted Wet area and screen with PID prior to resuming work Control with water spray HEPA = high efficiency particulate air PID = Photoionization Detector. ppm = parts per million February 2010 │ 215-2662-004 (01/03) 5 Project Health and Safety Plan Washington State Penitentiary Remedial Investigation/Feasibility Study Washington State Department of Corrections Table 3. Exposure Concentrations for Potential Chemicals of Concern Analyte Time Weighted 8-Hour, Permissible Exposure Limit Immediately Dangerous to Life and Health Benzene 1 ppm 500 ppm Ethylbenzene 100 ppm 800 ppm Toluene 100 ppm 500 ppm Xylene 100 ppm 900 ppm Arsenic 0.2 mg m Cadmium Chromium Lead 3 0.005 mg/m 0.5 mg/m 0.050 mg/m Mercury 0.1 mg/m 3 3 5 mg/m 3 9 mg/m 3 25 mg/m 3 3 3 100 mg/m 10 mg/m 3 3 Naphthalene and associated compounds 10 ppm 250 ppm Trichloroethylene 50 ppm 1,000 ppm Tetrachloroethylene 25 ppm 150 ppm Vinyl Chloride 1 ppm None Determined 300 ppm None Determined Gasoline Source: WAC 296-841 Table 3 (2007), NIOSH IDLH Program (1995) Notes: mg/m3 = micrograms per cubic meter ppm = parts per million 5. PERSONAL PROTECTIVE EQUIPMENT Based on available chemical information for the project sites, Level D PPE will be used for conducting sampling activities. If site conditions indicate a high level of protection is required, site personnel will be prepared to use Level C PPE. This level of protection generally includes: Level D 6 • • Steel-toe/shank leather or rubber boots/shoes. • • • • Nitrile surgical weight gloves to be used as inner gloves, as needed. • Hearing protection for all activities in areas where it is necessary to shout to communicate, or as decided. Coveralls, polycoated Tyvek suit, or equivalent, as needed for working with contaminated soil and water. Work gloves, nitrile gloves, or equivalent, to use as outer gloves, as needed. Hardhat. Safety glasses or goggles for general site work and with shading to control glare when working around water. February 2010│ 215-2662-004 (01/03) Project Health and Safety Plan Washington State Penitentiary Remedial Investigation/Feasibility Study Washington State Department of Corrections Level C • Steel-toe/shank leather or rubber boots/shoes. • Tyvek, Saranex, poly coated Tyvek, or equivalent coveralls, as needed for working with contaminated soil and water. • Nitrile surgical weight gloves to be used as inner gloves. • Work gloves, nitrile gloves, or equivalent, to use as outer gloves, as needed. • Hardhat. • Safety glasses or goggles for general site work and with shading to control glare when working around water. • Hearing protection for all activities in areas where it is necessary to shout to communicate, or as decided. • Full face air-purifying respirator. Additional information on PPE is presented the Parametrix Health and Safety Manual (Parametrix 2003) and Standard Operating Procedure HS-002, Appendix C of this document. At least one first aid kit and cellular phone will be available on-site in the company vehicle during onsite activities. 6. SITE CONTROL AND DECONTAMINATION Work site controls will be established whenever soil disturbance may take place. Non-intrusive inspections and other similar activities do not need hazardous waste site controls; however, there may be other crews with site zones established, and these shall be respected and maintained. It is anticipated that cones with tape barriers will be set up around areas of contaminated soil prior to and during excavation activities. The object of site control is to assure that only qualified personnel enter potentially hazardous locations and to effectively control the spread of contamination. As a minimum, a “hot” zone, extending approximately 10 feet from the work, should be established. If the sampling personnel are reasonably certain that untrained, unprotected people will not enter the “hot” zone, then demarcation may not be necessary. Barrier tape and cones will be used to demarcate contaminated soil prior to and during excavation activities. Only personnel with a current 40-hour Hazardous Waste Operation (HAZWOPER) certification and up-to-date refresher course will be allowed inside the restricted areas. The following items will be followed when establishing site control: • Site control measures shall be established prior to beginning any work that disturbs potentially contaminants soils. • Personnel will not enter vehicles with dirty boots, boot covers, or in dirty coveralls. Set the job up to keep the sediments in their original location on the site. • The work area shall be protected from public intrusion. • It is up to each sampling crew to establish site control based on potential hazards and on the crew’s planned activities. Make it practical and useful. • All tools used for sampling will be properly decontaminated after each use. Any potentially contaminated personnel will decontaminate prior to getting into vehicles, vessels, eating lunch, or leaving the site. February 2010 │ 215-2662-004 (01/03) 7 Project Health and Safety Plan Washington State Penitentiary Remedial Investigation/Feasibility Study Washington State Department of Corrections For all personnel working within a “hot” zone, decontamination will be conducted to remove gross contamination that may have accumulated on workers, equipment, and sampling supplies during site activities and to prevent the migration of contaminants from the site. Decontamination may consist of brushing with a stiff brush to remove dry particles and, if necessary, washing with household soap or an Alconox solution and rinsing with clean water. Additional information on decontamination procedures can be found in the Parametrix Health and Safety Manual (Parametrix 2003) and Standard Operating Procedure HS-007, Appendix C of this document. All water used for decontamination by personnel will be containerized and disposed of following site waste handling procedures or as described in the Parametrix Health and Safety Manual and Standard Operating Procedure HS-006, Appendix C of this document. 7. TRAINING All personnel conducting sampling activities on the project site must be HAZWOPER trained per the federal requirement 29 CFR 1910.120 and be current with their annual eight hour refresher course. All personnel should have proof of currency with HAZWOPER training requirements available on the project site. All personnel working at the project site will be briefed on potential site hazards, health and safety procedures, site construction rules and requirements, and sampling procedures. Following completion of this training, all personnel will be required to sign an acknowledgement form verifying that they have completed the project-specific health and safety training. A copy of the Project-Specific Training Acknowledgement Form is included in Appendix A. The Site Health and Safety Officer will conduct a tailgate safety meeting will be conducted each morning prior to the start of daily field activities. Each employee and, as appropriate, subcontractor personnel will attend the tailgate safety meeting and sign the daily tailgate meeting log. A Daily Tailgate Meeting Log is included in Appendix A. 8. PROJECT/EMERGENCY CONTACTS AND PROCEDURES The project and emergency contacts are shown in Table 4. These contacts will be updated as needed. Table 4. Project and Emergency Contacts Name 8 Role Phone Number Jack Olson Department of Corrections Environmental Manager (360) 725-8342 Mike Warfel Parametrix Project Manager (253) 863-5128 (425) 457-0621 (cell) Arnie Sugar HWA Project Manager (425) 774-0106 (ext. 227) To Be Determined SAR Safety Officer To Be Determined Field Sampling Staff To Be Determined Field Sampling Staff To Be Determined Field Sampling Staff Sheila McConnell Corporate Health and Safety Officer (425) 452-8655 (425) 681-7516 (cell) Emergency (fire, accident, etc.) – 911 Providence St. Mary Medical Center – (509) 525-3320 Poison Control Center – (800) 222-1222 February 2010│ 215-2662-004 (01/03) Project Health and Safety Plan Washington State Penitentiary Remedial Investigation/Feasibility Study Washington State Department of Corrections 8.1 EMERGENCY ASSISTANCE Table 4 provides a list of emergency telephone numbers. This list is to be in the possession of the Site Health and Safety Officer. At least one cell phone will be available onsite at all times during sampling activities. In the event of an emergency, 911 will be called immediately. If a non-emergency injury occurs that requires treatment, refer to the map and directions to the nearest hospital (Providence St. Mary Medical Center) in Appendix B. 8.2 POTENTIAL INCIDENTS Although considered unlikely, the following situations could occur and would require an emergency response action: • • • • • Sudden release of hazardous vapors/combustible gases. Problems due to contacting utility lines (gas, electric, water). Fire. Medical emergency. Overt exposure (skin contact, inhalation, ingestion). Release of Hazardous Vapors/Combustible Gases In the event of a sudden release of hazardous vapors or gases constituting a potentially hazardous situation (e.g., adequate respiratory protection is unavailable, atmospheres are immediately dangerous to life or health or explosive, there is an imminent public health and safety hazard), the Site Health and Safety Officer will suspend operations and evacuate the site, and call 911. All personnel will be required to evacuate to a pre-designated safe area upwind of the release. The Field Health and Safety Officer, in consultation with the emergency response agencies, fire department, and facility or system owner/operator, will attempt to control or secure the spread of contamination whenever possible. Utilities If aboveground or underground utilities are damaged or contacted, call 911 to notify the local fire department. If injury occurs, see Medical Emergency section below. Fire In the event of a fire, call 911. Medical Emergency At least one Parametrix employee or onsite worker will have current certification in first aid and cardiopulmonary resuscitation (CPR). In the event of a serious injury or illness, call 911 immediately. For non life threatening injuries that do not impair driving ability, site personnel will drive to Providence St. Mary Medical Center in Walla Walla. Appendix B illustrates the route to the hospital. A first aid kit will be available at the site for use in case of minor injuries. First aid responders should protect themselves from contact with blood and other human body fluids by wearing latex gloves or establishing an equivalent barrier. Any contact with blood should be reported to the Site Health and Safety Officer. February 2010 │ 215-2662-004 (01/03) 9 Project Health and Safety Plan Washington State Penitentiary Remedial Investigation/Feasibility Study Washington State Department of Corrections Exposure In the event of respiratory exposure, dermal or eye contact, or ingestion, the following procedures will be followed: • Respiratory Exposure (Inhalation). Move to fresh air. Summon paramedics and notify facility or system owner/operator. Any loss of consciousness or exposure to elevated levels of known toxic contaminants, even if the individual appears to have fully recovered, will require immediate treatment and/or surveillance by a qualified physician. • Dermal Contact. Flush area with copious amounts of soap and water. Wash/rinse affected area for at least 15 minutes. Decontaminate and provide medical attention. • Eye Contact. Flush eye(s) for a period of 15 minutes and transport worker to the nearest emergency medical facility. Treatment and/or surveillance by a qualified physician are required. • Ingestion. Notify the local Poison Control Center and/or emergency medical facility and immediately transport to the facility. 8.3 ADVERSE WEATHER CONDITIONS In the event of adverse weather conditions, the Field Health and Safety Officer will determine if sampling activities can continue without endangering field personnel. Some of the conditions to be considered prior to determining if activities should continue are as follows: 9. • • Potential for thermal stress (e.g., heat or cold stress) and related injuries. • • Limited visibility. Dangerous weather related working conditions that would preclude working from a boat (e.g., high winds, rain, snow, fog, lightning, etc.). Potential for electrical storms. No outside activities will be permitted during electrical storms. STANDARD OPERATING PROCEDURES The following project-related standard operating procedures (SOPs) are included in Appendix C: 10 • Personal Protective Equipment (SOP HS-002). • • • • Respiratory Protection (SOP HS-003). Handling of Investigation Derived Waste (SOP HS-006). Decontamination (SOP HS-007). Heat Stress (SOP HS-010). February 2010│ 215-2662-004 (01/03) Project Health and Safety Plan Washington State Penitentiary Remedial Investigation/Feasibility Study Washington State Department of Corrections 10. REFERENCES National Institute for Occupational Safety and Health (NIOSH). 1994. Documentation for immediately dangerous to life or health concentrations (IDLH): NIOSH chemical listing and documentation of revised IDLH values (as of 3/1/1995). Available at <http://www.cdc.gov/niosh/idlh/intridl4.html>. National Institute of Safety and Health (NIOSH). 2005. Pocket guide to chemical hazards. September. www.cdc.gov/niosh/npg Parametrix. 2003. Parametrix health and safety manual. Prepared for EPA Region X. March. Washington Administrative Code 296-841. Department of Labor and Industries, Division of Occupational Safety and Health. Airborne contaminants. April 2007 Edition. February 2010 │ 215-2662-004 (01/03) 11 APPENDIX A Forms PROJECT-SPECIFIC TRAINING ACKNOWLEDGEMENT FORM FOR HAZARDOUS WASTE OPERATIONS Prior to the initiation of field activities, I attended a site-specific training for the Palermo Groundwater Long-term Monitoring Project. The training included topics that are covered in the Parametrix Health and Safety Manual and the project-specific Health and Safety Plan (HASP). Additionally, I have been given an opportunity to read and questions the contents of these documents. By signature, I certify that I have read, understood, and agree to comply with the information and directions set forth in the aforementioned documents and site-specific training. I further certify that I am in full compliance with OSHA 29 CFR 1910.120 in regards to training and medical monitoring requirements, as well as all other federal, state, and local regulations in regards to training and medical requirements. SITE SPECIFIC OPERATIONS, POTENTIAL HAZARDS, AND CONTROL PRINTED NAME SIGNATURE DATE: MEETING LOCATION: TRAINER: TITLE: COMMENTS/EXCEPTIONS/EXEMPTIONS: TRAINER SIGNATURE: TRAINING DATE PARAMETRIX DAILY HEALTH AND SAFETY TAILGATE MEETING LOG DATE/TIME NAME (PRINT) NAME (SIGNATURE) TOPIC APPENDIX B Map and Directions to Hospital 1313 N 13th Ave, Walla Walla, WA 99362 to 401 W Poplar St, Walla Walla, WA 99362 - Google ... Page 1 of 2 Directions to 401 W Poplar St, Walla Walla, WA 99362 1.8 mi – about 5 mins Loading... ©2010 Google - Map data ©2010 Google - http://maps.google.com/maps?f=d&source=s_d&saddr=1313+West+13th+St+Walla+Walla+WA&d... 2/25/2010 1313 N 13th Ave, Walla Walla, WA 99362 to 401 W Poplar St, Walla Walla, WA 99362 - Google ... Page 2 of 2 1313 N 13th Ave, Walla Walla, WA 99362 1. Head south on N 13th Ave/WA-125 S toward Carrie Ave Continue to follow N 13th Ave About 2 mins go 1.1 mi total 1.1 mi 2. Turn left at W Rose St About 2 mins go 0.4 mi total 1.6 mi 3. Turn right at S 7th Ave About 1 min go 0.2 mi total 1.8 mi 4. Take the 3rd left onto W Poplar St Destination will be on the right go 371 ft total 1.8 mi 401 W Poplar St, Walla Walla, WA 99362 These directions are for planning purposes only. You may find that construction projects, traffic, weather, or other events may cause conditions to differ from the map results, and you should plan your route accordingly. You must obey all signs or notices regarding your route. Map data ©2010 Google Directions weren't right? Please find your route on maps.google.com and click "Report a problem" at the bottom left. http://maps.google.com/maps?f=d&source=s_d&saddr=1313+West+13th+St+Walla+Walla+WA&d... 2/25/2010 APPENDIX C Standard Operating Procedures SOP HS-002 Parametrix Issued: March 12, 2003 Revision No.1 Page 1 of 3 ENGINEERING. PLAN .... ING • ENVIRONMI:NTAL SCIENCES PERSONAL PROTECTIVE EQUIPMENT Date: 3- I () ... () 3. Date: Reviewed By: Approved By: Date: Chief Operating Officer 1.0 Purpose This Standard Operating Procedure (SOP) establishes guidelines for selection and use of Personal Protective Equipment (PPE) used to protect Parametrix employees from the risk of injury by creating a barrier against workplace hazards. 2.0 Scope 29 CFR 1910, SUbpart I requires the use of PPE to reduce employees' exposures to hazards when engineering and administrative controls are not feasible or effective in reducing these exposures to acceptable levels. Employers are required to determine all exposures to hazards in their workplace and determine if PPE should be used to protect their workers. OSHA requires employers to conduct inspections of all workplaces to determine the need for PPE and to help in selecting the proper PPE for each task performed. This SOP addresses eye, face, head, foot, hand, and body protection. discussed in SOP HS~003. 3.0 Respiratory protection is Responsibilities There are specific responsibilities for Parametrix personnel in the care and use of PPE, depending on an individual's role within the company or on a given project. These responsibilities are outlined below: • Corporate Health and Safety Officer (CHSO): The Corporate Health and Safety Officer is responsible for developing the PPE Program and updating PPE procedures, as necessary. • Project Manager: The Project Manager is responsible for field implementation of the PPE Program. This includes assurance that all personnel on site comply with the policy and that all on-site personnel have had proper training in using PPE . • Site-specific Health and Safety Officer (SHSO): The Site-specific Health and Safety Officer is responsible for initial on-site coordination of the cold stress. The SHSO assures that all personal potentially exposed to potential environmental hazards have proper PPE. • Team Member: Each Team Member is responsible for understanding and complying with all site requirements. :~::,.::~~ .,(:-:~ .~ ... "~:'i.'~1.': '.J SOP Parametrix HS~002 I ssued: March 12, 2003 Revision No. 1 Page 2 of 3 ENGI .... eERING • Pl.ANNING • ENViRONMENTAL SCIENcES PERSONAL PROTECTIVE EQUIPMENT 4.0 Requirements Eye and Face Protection Eye and face protection shall be used when employees are exposed to potential hazards from flying particles, molten metal, acids or caustic liquids, chemicals, or gases. Eye and face protection requirements include: • Appropriate eye and face protection devices in hazardous environments for personnel who wear contact lenses. • Side protectors when there is a hazard from flying objects. • Goggles and face shields when there is a hazard from chemical splash. • Face shields worn only over primary eye protection (safety glasses or goggles). • Eye protectors that incorporate an employee's corrective eye prescription in the design or that fit properly over the prescription lenses. Emergency eyewash facilities meeting the requirements of ANSI Z358.1 will be provided in all areas where the eyes of any employee may be exposed to corrosive materials. All such emergency facilities will be located where they are easily accessible in an emergency. Protective eye and face devices purchased after July 5, 1994 shall comply with ANSI Z87.1-1989, "American National Standard Practice for Occupational and Educational Eye and Face Protection." Head Protection Head protection (hard hat) must be worn by all employees when overhead hazards from falling or fixed objects are present. Also, when an employee is near exposed electrical conductors that could come in contact with the head, the employee must wear a protective helmet designed to reduce electrical shock hazard. ''!.·'::~'n:~.~ Protective headgear shall comply with ANSI Z89.1-1986, "American National Standard for Personnel Protection-Protective Headwear for Industrial Workers-Requirements." ,~ -""ry'.!J~ " z.:-.;~·;:~ Foot Protection ~!.~l.~. :.- .;'l-~}¥~j Steel-toed boots or shoes must be worn in work areas where carrying or handling materials such as packages, objects, parts, or heavy tools could be dropped or fall onto the feet. Safety shoes or boots with puncture protection are required where sharp objects such as nails, wire, tacks, screws, large staples, scrap metal, etc., could be stepped on by employees and cause foot injury. When working with hazardous chemicals or waste, chemical-resistant, steel-toed boots may be required. All safety footwear shall comply with ANSI Z41-1991, "American National Standard for Personal Protection - Protective Footwear." SOP Parametrix ENGINEERING. PI.ANNING III HS~002 Issued: March 12, 2003 Revision No.1 Page 3 of3 ENVJRONMENTAL SCIENCES PERSONAL PROTECTIVE EQUIPMENT Hand Protection Suitable gloves shall be worn when hazards from chemicals, cuts, lacerations, abrasions, punctures, burns, and other hazards to the hands are present. Glove selection shall be based on performance characteristics of the gloves, conditions, durations of use, and hazards present. The first consideration in the selection of gloves for use against chemicals is to determine, if possible, the nature of the substances to be encountered. Employees must read instructions and warnings on chemical container labels and MSDSs before working with any chemical. Body Protection Suitable body protection (torso and legs) must be worn while completing job tasks. Depending on the hazards present, body protection may include coveralls, Tyvek or Saranex suits, totally encapsulating suits, etc. The type of body protection required to perform a specific task will be determined by the Corporate or Site-specific Health and Safety Officer, as necessary. 5.0 Training Any worker required to wear PPE shall receive training in the proper use and care of PPE. The training shall include, but not necessarily be limited to, the following subjects: • Determining when wearing PPE is necessary. • Determining the appropriate and necessary PPE. • Learning how to properly wear, adjust, and remove PPE. • Understanding the limitations of PPE. • Understanding the proper care, maintenance, and disposal of PPE. References 'T<""'~\ '.;":'i":J ~~~~'7;;; ,.: • • • 0. U.S. Department of Labor, OSHA Standard 29 CFR 1910, Subpart I. SOP HS-003 Parametrix Issued: March 12, 2003 Revision No.1 Page 1 of 11 eNGINeeRING. PLANNING. ENVIRONMeNTAL SCIENCES RESPIRATORY PROTECTION PROGRAM Date: 1.0 Reviewed By: Date: Approved By: Date: j-It) -cJ.Y Purpose To establish the minimum requirements for Parametrix, Inc. employees to use respiratory protection. 2.0 Scope This Standard Operating Procedure (SOP) applies in its entirety to all Parametrix projects unless the Corporate Health and Safety Officer (CHSO) grants a variance. 3.0 Responsibilities There are specific responsibilities for Parametrix personnel in complying with the Respiratory Protection Program, depending on an individual's role within the company or on a given project. These responsibilities are outlined below: • Project Manager: Overall responsible for establishing and ensuring compliance with this procedure. -'>'·i''''''~ • Field Health and Safety Staff: associated with this procedure. ~~~~~ • Managers and Supervisory Personnel: Responsible for enforcing this procedure and ensuring that each employee is properly following the procedure. to ~ \,. \ :5: ·w ~~*~~~ , ~':'~~t \~'1,.:.:.~;;~. Responsible for. implementing and/or monitoring activities ....Ji:-:-\~~ l;~,). 4.0 General Requirements ~;?~~~ Respirator wearers cannot be afforded protection from hazardous airborne contaminants when conditions prevent a complete gas-tight face seat. Facial hair, head hair, and eyeglasses are among these physical obstructions. While eyeglasses are in the category of obstructions that prevent a gas-tight face seal, primarily in the case of full-face supplied-air respirators, this problem is correctable by using mounting devices to hold the eyeglass frames inside the respirator face piece. The criteria state that there can be no obstruction of contact between the wearer's skin and the mask. Beard stubble constitutes a physical obstruction. Affected employees shall be required to be clean-shaven, as a condition of employment. SOP HS-003 Parametrix ENGINEERING 'II Issued: March 12, 2003 Revision No.1 Page 2 of 11 PLANNING. ENVIRONMENTAL SCIeNCES RESPIRATORY PROTECTION PROGRAM Candidates for employment who object to this policy shall be made aware that their versatility on work assignments may be limited and that this factor can affect their job assignments. Parametrix shall provide respirators whenever a qualified person determines that such equipment is necessary to protect the health of the employee from significant inhalation exposure. Only respirator equipment that has been jointly approved by the Mine Safety and Health Administration (MSHA) and the National Institute for Occupational Safety and Health (NIOSH) shall be provided. Employees shall be instructed and trained in the need, use, sanitary care, and limitations of such respiratory equipment prior to being assigned to activities that require respiratory protection. Parametrix shall provide, repair, or replace respiratory protective equipment as may be required due to wear and deterioration. Means of cleaning all respiratory protective equipment shall be provided. Only those employees who are trained and medically qualified to wear respirators shall be assigned to work requiring use of respirators. 5.0 Implementation Respiratory Selection When respirator use is required, only properly cleaned and maintained NIOSH/MSHA~approved respirators shall be used. Single-use respirators (dust masks) may only be used with specific approval by the Corporate Health and Safety Officer. Employees shall be allowed to pick the most comfortable respirator from a selection, including respirators of various sizes from different manufacturers. Selection of respirators shall be approved by the Field Health and Safety Staff in all cases. and shall be based on the following considerations: ~::;-;~~,~ :i • Nature of the Hazard - The chemical and physical properties, toxicity, and concentration of hazardous material or mixture of materials. • Oxygen-deficient Atmospheres - Entry into oxygen-deficient atmospheres is prohibited without prior approval of the Corporate Health and Safety Officer. • Immediate Dangerous to Life and Health (IDLH) Atmospheres - Entry into any IDLH atmosphere is prohibited without prior approval of the Corporate Health and Safety Officer. • Irritant or Corrosive Atmospheres - Respirators selected must prOVide adequate face and eye protection. The contaminant or mixture of contaminants must have adequate warning properties (odor, irritation, or taste) to indicate respirator breakthrough if an air-purifying device is used. \<:'1',:), '~"7?.t1r~ \,.., ) "~~";1 '~:~';~~1 SOP HS·003 Parametrix Issued: March 12, 2003 Revision No.1 Page 3 of 11 ENGINEERING. PLANNIN.G. EN:VIRONMENTAL SCIENCES RESPIRATORY PROTECTION PROGRAM • Regulated Materials - In all cases where OSHA has required that a specific respirator is used (carcinogen standards, etc.), the specified respirator, or one providing equal or better protection, shall be used. • Air-purifying respirators shall NOT be used for protection against the materials listed below. Note that this is only a partial list; please contact the Field Health and Safety Staff for further information: Acrolein Methyl chloride Aniline Methylene chloride Arsine Nickel carbonyl Bromine Nitrobenzene Carbon monoxide Nitrogen oxides Ol1socyanates Nitroglycerine Dimethylaniline Nitromethane Dimethyl sulfate Ozone Hydrogen cyanide Phosgene Hydrogen fluoride Phosphine Hydrogen selenide Phosphorus trichloride Hydrogen sulfide Stibine Methanol Sulfur chloride Methyl bromide Parametrix subcontracts most asbestos inspections and all asbestos abatement. Inspection personnel may use half-mask respirators in areas where asbestos is present if they are qualitatively-fit tested. Full-facepiece, negative-pressure, air-purifying respirators are not acceptable for protection against asbestos exposure unless the wearer meets the quantitative fit testing requirement. Use of Corrective Lens Eyewear with Respirators The wearing of contact lenses in work environments that involve exposure to chemical fumes, vapors, splashes, intense heat, molten metals, or highly particulate-contaminated atmosphere is prohibited. ..... ., ~ .'.~ .~i Management shall assess which employees in their operations wear eye glasses routinely, determine what respiratory protective masks (makes and models) are used, and assure that the appropriate frames or ophthalmic device hangers are obtained and provided at company expense. SOP HS-003 Parametrix Issued: March 12,2003 Revision No.1 Page 4 of 11 ENGINEERING .. PLANNING, ENVIRONMENTAL SCIENCES RESPIRATORY PROTECTION PROGRAM Employee Training and Instruction The basic respiratory training program shall include, as a minimum, the foHowing: '1 ~"'("',,,;i. l .; • Instruction in the need for, use, sanitary care, and limitations of each respirator type. • Opportunity for "hands-on" experience with respirators. • Proper fitting, including demonstrations and practice in wearing, adjusting, and determining the fit of the respirator. A selection of respirators shall be available to determine the most comfortable respirator and the best fit. • How to perform a positive and negative pressure test of the face piece to face seal. • A familiarization period of wear in normal air. • For negative pressure respirators, qualitative fit testing will be conducted by wearing the respirator in an irritant fume test atmosphere. A qualified person using the protocol found in Attachment A of this procedure shall perform all qualitative fit testing or other protocol, as designated by specific standards (e.g., asbestos, benzene). Powered air-purifying respirators (PAPRs) shaH be worn in a test atmosphere with the power supply disconnected to evaluate fit in the negative pressure modes. • Qualitative fit testing shall be performed annually, or more frequently as required by law. Quantitative fit testing may be required for some respirator or contaminants. The Field Health and Safety Staff will determine fit test requirements. Fit testing procedures are presented in Attachment A. • Instruction in the nature of the respiratory hazards, whether acute, chronic, or both, and a description of potential health effects jf the respirators are not used. • Classroom and field training to recognize and cope with emergency situations (including respirator failure). Training provided as part of this procedure shall be performed in accordance with applicable regulations. '. ...~~~~ Respirator Inspection, Cleaning, Maintenance, and Storage ~~'l,;; , ?::~~$ <:"'T;;")l General: The Field Health and Safety Staff will define and provide a program to area/facility management regarding maintenance and care of respirators, and which shall be adjusted to the type of facility, working conditions, and hazards involved. This program shall include the following basic elements: • Inspection for defects and/or deterioration. • Cleaning and disinfecting in accordance with manufacturers' instruction. • Repair, as necessary. SOP HS-003 Parametrix ENGINEERlNG • PLANNING. ENVIRONMENTAL sCU!NCES Issued: March 12, 2003 Revision No.1 Page 5 of 11 RESPIRATORY PROTECTION PROGRAM • Establishment and maintenance of a record-keeping system to document respiratory inspection, repair, and maintenance. • Proper storage. Inspection, Maintenance, and Storage Users shall inspect all respirators routinely before, during, and after each use. Any defects shall be reported to the supervisor. No defective respirators shall be issued or worn. Defective respirators shall be tagged and returned for repair. Respirators maintained for emergency use (such as SCBA) shall be inspected and sanitized after each use and inspected at least monthly. A record of the most recent inspection shall be maintained on the respirator or the storage container and shall include the inspector's identification, the date, and a respirator identification number. An individual who is qualified by experience or training shall regularly clean, inspect, and sanitize routinely-used respiratory equipment. Other types of respiratory equipment shall be maintained according to the manufacturers' instructions. Where respirators are assigned to individual employees, area management shall ensure compliance with cleaning and maintenance requirements by periodically inspecting respiratory equipment and conducting field audits. Respiratory equipment shall not be passed from one person to another until it has been cleaned and sanitized. When not in use, respirators 'shall be stored to protect against dust, sunlight, extreme temperatures, excessive moisture, damaging chemicals, and physical damage. Air Purifying Respirators (APR) Fit testing shall be accomplished In accordance with Attachment A of this procedure. When APRs are worn, employees shall change the filter-cartridge elements daily, in the case of cartridges used for non-particulate contaminants, or sooner if "breakthrough" is occurring. For other filter cartridges, the filter-cartridge should be replaced whenever an increase in breathing resistance is detected. "~. 't::~~ .{~:;} ~~;:..~ Powered Air Purifying Respirators (PAPR) When PAPRs are worn, employees shall change filter/cartridge elements dally, in the case of cartridges used for non-particulate contaminants, or sooner if "breakthrough" is occurring. For other filter cartridges, the filter-cartridge should be replaced if any of the following scenarios occur: SOP HS·003 Parametrix Issued: March 12,2003 Revision No.1 Page 6 of 11 eNGINEERING. PL.ANNtNG • ENViRONMENTAL SCIENces RESPIRATORY PROTECTION PROGRAM • Whenever an increase in breathing resistance is detected, or • When airflow through filter elements decreases to an unacceptable level, as indicated by the manufacturer's test device. Compressed Air Systems • Air Quality }> Compressed air used for respiration shall be of high purity, and shall meet, as a minimum, the requirements for the specification for Grade 0 or better breathing air as described in Compressed Gas Association Specification G-7,1 (ANSI Z86.1-1973). The supplier shall certify compliance with these reqUirements for each lot of breathing air supplied. }> Breathing air shall be free from harmful dusts, fumes, mists, vapors, gases, or odors. }> Oxygen shall NOT be used at any time in open-circuit SCBAs or in air-line respirators. . }> Mixed or blended air shall not be used for breathing purposes. Compressed Air Cylinder Systems (Cascade) Breathing air cylinders shall be legibly identified with the word AIR, by means of stenciling, stamping, or labeling as near to the valve end as practical. Cascade systems shall be equipped with low-pressure warning bells or similar warning devices to indicate air pressure in the manifold below 500 psi. When a cascade system is used to supply breathing air, one employee shall be assigned as a safety standby within audible range of the low- pressure alarm. When a cascade system is used to recharge SCBA air cylinders, it shall be eqUipped with a high-pressure supply hose and a coupling rated at a capacity of at least 3,000 psi. .'I!~)~;~ ,\",} '~~, Air-line couplings shall be incompatible with outlets for other gas systems to prevent inadvertently supplying air-line respirators with non-respirable gases or oxygen. The air pressure at the hose connection to positive pressure respiratory equipment shall be within the range specified in the approval of the eqUipment by the manufacturer. Cylinders shall be stored and handled to prevent damage to the cylinder or valve. Cylinders shall be stored upright with the protective valve cover in place and, in such a way (e.g., supported with substantial rope or chain in the upper one-third of the cylinder, or in racks designed for this purpose) as to prevent the cylinder from falling. Cylinders shall not be dropped, dragged, rolled, or allowed to strike each other or to be struck violently. Cylinders shall never be exposed to temperatures exceeding 125°F. Cylinders with visible external damage, evidence of corrosion damage, or exposure to fire shall not be accepted or used. Only cylinders within current hydrostatic test periods shall be used. SOP HS-003 Parametrix ENGINEERING. PLANNING. ENVIRONMENTAl. SCIIlNCES Issued: March 12, 2003 Revision No.1 Page 7 of 11 RESPIRATORY PROTECTION PROGRAM Compressor Supplied Breathing Air All compressors used for supplying breathing air shall be equipped with the following safety and standby devices: • Compressor intakes that are located to ensure that only respirable (uncontaminated) air is admitted. This requires attention to the location of the compressor intake with respect to compressor engine exhaust, chemical storage or use areas, and suitable intake screening or filtration. • Alarms to indicate compressor failure (such as low-pressure air horns, etc.) shall be installed in the system. • A receiver of sufficient capacity to enable the respirator wearer to exit from a contaminated atmosphere upon compressor failure shall be provided. • Oil Lubricated Compressors - If an oil-lubricated compressor is used to supply breathing air, it shall be equipped with both of the following devices: » A continuous-reading carbon monoxide monitoring system that is set to alarm should the carbon monoxide concentration exceed 10 ppm. » A high-temperature alarm which will activate when the discharge air exceeds 110% of the normal operating temperature in degrees Fahrenheit, • A designated employee shall be assigned as a safety standby and shall remain continuously within audible range of the alarms. • An inline purifying filter assembly to remove oil, condensed water, particulate, odors, and organic vapors shall be used in conjunction with the air compressor. Routine inspection and maintenance of the air compressor shall be performed in accordance with manufacturer's specifications. ~ '>0-. . Escape/Egress Units '1">'."fj \,,J These respirators are intended for use in areas where escape with a short-term (5-10 minute) air supply is necessary. They may be used as adjuncts to airline pressure demand respirators as a backup air supply; or as independent emergency devices in areas where respiratory protection is not normally required. Appropriate training shall be accomplished and documented prior to assigning employees to tasks or locations subject to the use of these respirators. Escape/egress units shall never be used as primary standby respirators for confined space entry. SOP HS·003 Parametrix ENGINEERING. PLANNING. ENVIRONMEHTAL. SCIENces Issued: March 12, 2003 Revision No.1 Page 8 of11 RESPIRATORY PROTECTION PROGRAM Medical Screening All potential candidates shall complete a medical questionnaire prior to respiratory use and once every three years. A more comprehensive medical evaluation may be reqUired based on the results of the questionnaire. No employee shall be assigned to a task that requires the use of a respirator unless it has been determined that the employee is physically able to perform the work while using the required respirator. If an employee demonstrates difficulty in breathing during the fitting test or during use, the employee shall be re-examined by a physician to determine whether the employee can wear a respirator while performing the required duty. Once a medical determination has been made to physical ability to wear a respirator, a review of the employee's health status shall be conducted annually, at a minimum. SOP Parametrix HS~003 Issued: March 12, 2003 Revision No.1 Page 9 of 11 ENGINEERING. PLAPfNING • I:NVlRONMENTJl1. SCIE:N:C:e:S RESPIRATORY PROTECTION PROGRAM ATTACHMENT A PARAMETRIX MANDATORY QUALITATIVE RESPIRATOR FIT TEST PROTOCOL NOTE: This protocol does not satisfy the fit test requirements for certain materials, including asbestos and benzene. Contact the Field Health and Safety Staff for assistance. Respirator Selection Respirators shall be selected as described in this procedure. The respirator shall be equipped with HEPA filters. Fit Test The test conductor shall review this protocol with the test subject before testing. The test subject shall perform the following conventional positive and negative pressure fit checks: • Negative Pressure Test - Cover the cartridge filter inlets with your palm and gently inhale, the face piece should collapse against the face. • Positive Pressure Test - Cover the exhalation valve cover with your palm and gently exhale. The face piece should expand away from the face. • If either test fails, loosen and readjust the respirator straps and check for obstructions to the sealing surface. Repeat both tests. If the test fails again, select an alternate respirator. A test atmosphere shall be generated with irritant smoke. The test subject shall be advised that the smoke can be irritating to the eyes and instructed to keep the eyes closed while the test Is being conducted (applies to half-mask respirators). While wearing the selected respirator, the test subject shall enter the test atmosphere and perform the following exercises: \:'~;~<i1:l:!:!:\ ,>~,~b • Breathe normally, • Breathe deeply. Be certain breaths are deep and regular. • Turn head all the way from one side to the other. Be certain movement is complete. Inhale on each side. Do not bump the respirator against the shoulders. • Nod head up and down, Be certain motions are complete and made every second. Inhale on each side. Do not bump the respirator against the shoulders. • Nod head up and down, Be certain motions are complete and made every second. Inhale when head is in the full, up position (looking toward coiling). Do not bump the respirator against the chest. \~:;"l~ sop HS-003 Parametrix Issued: March 12, 2003 Revision No.1 ENGINEERING. Pl.ANNING. • ENVUtoNMENTAL SCIENCEs Page 10 of 11 RESPIRATORY PROTECTION PROGRAM • Talk aloud and slowly in a fashion that will generate a wide range of facial movements. • Breathe normally. The test subject shall indicate to the test conductor if the irritant smoke is detected, If smoke is detected, the test conductor shall stop the test. In this case, the tested respirator is rejected and another respirator shall be selected. Each test subject passing the smoke test (Le., without detecting the smoke) shall be given a sensitivity check of smoke from the same tube to determ ine if the test subject reacts to the smoke. This may be performed by cracking the mask and gently inhaling while inside the test atmosphere. Failure to evoke a response shall void the fit test. This may trigger an asthmatic response; verify before beginning. The test shaH not be conducted if there is any hair growth between the skin and the face-piece sealing surface. If hair growth or apparel interferes with a satisfactory fit, then the obstruction(s) shall be altered or removed to eliminate interference and allow a satisfactory fit. If a satisfactory fit is still not attained, the test subject must use a pOSitive-pressure respirator, such as a powered, air-purifying respirator, supplied air respirator, or self-contained breathing apparatus, If a test subject exhibits difficulty in breathing during the tests, the subject shall be referred to a physician trained in respiratory diseases or pulmonary medicine to determine whether the test subject can wear a respirator while performing required duties. Qualitative fit testing shall be repeated at least every year, or more often, as required by law. In addition, because the sealing of the respirator may be affected, qualitative fit testing shaH be repeated immediately when the last subject has experienced: • A weight change of 20 pounds or more. • Significant facial scarring in the area of the • Significant dental changes (Le., multiple extractions without prosthesis, or acquisition of dentures). • Reconstructive or cosmetic surgery. • Any other conditions that may interfere with face-piece sealing. 'I " face~piece seal. '.~~;.~~ ~t'..···:'r~j SOP HS-003 Parametrix ENGINEERING. PLANNING. eNVIRONMENTAL SCiENCES Issued: March 12,2003 Revision No.1 Page 110111 RESPIRATORY PROTECTION PROGRAM Record Keeping The following fit test forms shall be maintained in each office for three years. The Corporate Health and Safety Officer shall maintain permanent records. The summary shall include: • Name of test subject. • Date of testing. • Name of test conductor. • Respirator selected (indicate manufacturer, model, size, and approval number). • Testing agent.